Diffusion welding. Typical technological process of diffusion welding in vacuum
A distinctive feature of diffusion welding from other methods of pressure welding is the relatively high heating temperatures (0.5-0.7 Tm) and comparatively low specific compressive pressures (0.5-0 MPa) with isothermal exposure from several minutes to several hours.
The formation of a diffusion bond is determined by such physicochemical processes occurring during welding, as the interaction of heated metal with ambient gases, cleaning of welded surfaces from oxides, development of high-temperature creep and recrystallization. In most cases, these are diffusion, thermally activated processes.
To reduce the rate of oxidation of welded workpieces and create conditions for cleaning contact surfaces from oxides, reducing gases, melts of salts, fluxes, and coatings can be used in welding, but in most cases vacuum or inert gases are used.
Cleaning of metal surfaces from oxides can occur as a result of the development of sublimation and dissociation of oxides, dissolution of oxides due to the diffusion of oxygen into the metal (metal ions into the oxide), reduction of oxides by deoxidizing elements contained in the alloy and diffusing on heating to the metal-oxide interface . Calculation and experiment show that, for example, on steel, oxides are removed most intensively by their reduction by carbon, and on titanium by the dissolution of oxygen in the metal.
Approximation of welded surfaces occurs primarily as a result of plastic deformation of microprotrusions and near-surface layers caused by application of external compressive stresses and heating of the metal. In the process of deformation of welded surfaces free from oxides, their activation takes place, and when the physical contact between such surfaces develops, their setting is realized.
When diffusion welding of like metals welded joint achieves an even strength of the base material in the case where the structure of the bond zone does not differ from the structure of the base material. To do this, common in the contact zone for the materials to be joined is grain. This is possible due to migration of grain boundaries, either by primary recrystallization or by collective recrystallization.
With the help of diffusion welding in vacuum, high-quality ceramic compounds are obtained with the kovar, copper, titanium, refractory and refractory metals and alloys, electrovacuum glasses, optical ceramics, sapphire, graphite with metals, composite and powder materials.
The joints can be quite different in shape and have compact contact surfaces (Figure 3.66, a) or developed contact surfaces (Fig. 3.66, b, c). The geometric dimensions of the parts to be welded are in the range of several micrometers (in the manufacture of semiconductor devices) up to several meters (in the manufacture of laminated structures).
Fig. 3.66. Some types of structures produced by diffusion welding
Schematically, the diffusion welding process can be represented as follows. The welded blanks are assembled in a device that allows pressure to be transferred to the joint zone, evacuated and heated to the welding temperature. After that, a compressive pressure is applied for a predetermined period of time. In some cases, after depressurization, the article is additionally maintained at the welding temperature for a more complete flow of recrystallization processes that promote the formation of a benign compound. At the end of the welding cycle, the assembly is cooled in a vacuum, inert atmosphere or air, depending on the type of equipment.
Depending on the stresses causing metal deformation in the contact zone and determining the process of formation of the diffusion bond, it is advisable to differentiate between welding with a high-intensity (P ≥ 20 MPa) and low-intensity (P ≤ 2 MPa) force action. When welding with a high-intensity action, the welding pressure is usually created by a press equipped with a vacuum chamber and a heating device (Figure 3.67). But on such installations it is possible to weld parts of limited dimensions (as a rule, up to 80 mm in diameter (see Figure 3.66, a) .We use open presses when manufacturing large-sized double-layer structures (see Figure 3.66, b). the press is collected in sealed containers, which are evacuated and heated to a welding temperature (Figure 3.68).
Fig. 3.67. Schematic diagram of the installation for diffusion welding (a) and general form multi-position installation SDVU-4M (b): and 1 - vacuum chamber; 2 - camera cooling system; 3 - vacuum system; 4 - high-frequency generator; 5 - hydraulic press system
To exclude the possibility of loss of stability of welded elements, transfer of pressure to the welding zone and creation of conditions for locally directed deformation of the weld metal in the joint area, diffusion welding is carried out in devices using technological inserts and blocks to fill the "voids" (intercostal spaces) (see Figure 3.68 ), which, after welding, are dismantled or removed by chemical etching.
Fig. 3.68. Technological scheme of diffusion welding with high-intensity force:
a is the required construction; b - billets for welding; в - technological elements-loose leaves; d - assembly; d - welding in the press; e - dismantling; ж-ready construction; 1 - technological inserts; 2-technological container; 3 - press
When welding with high-intensity force, the local deformation of the metal in the joint zone, as a rule, reaches several tens of percent, which ensures a stable production of a benign compound.
For the production of layered structures (see Figure 3.66, c), diffusion welding with low-intensity force is promising, at which the allowable compressive forces are limited by the stability of thin-walled elements. This method of diffusion welding does not require complicated special equipment.
In the production of flat (or with a large radius of curvature), the compressive force can most easily be achieved by atmospheric air pressure Q on the outer surface of the tooling when the gas pressure in the joint zone decreases (Figure 3.69).
Fig. 3.69. Technological scheme of diffusion welding with low-intensity force action of flat structures:
a is the required construction; b - billets for welding; в - assembly; r - welding; d - finished structure; 1 - supporting sheathing; 2 - finished aggregate; 3 - technological sheets; 4 - membrane
The presence of technological elements (gaskets, membranes, etc.), having local rigidity and placed on the outside of the welded elements, excludes the possibility of loss of stability of the shells in the form of deflections of unsupported sections. The value of the welding pressure P is limited by the limiting stress of loss of stability of the aggregate σ p.s. (P ≤ σ p.z.).
When manufacturing structures of a complex curvilinear profile, a technological scheme can be used (Figure 3.70), in which the pressure of the neutral gas is directly perceived by the external elements of the structure itself, for example, bearing shells, shells. In the process of welding, the shells on deformed areas under pressure of gas deform (bend). This worsens the conditions for the formation of the joint, reduces the cross-section of the communicating channels, and worsens the aerodynamic state of the surface. In this case, P is limited by the stress at which there is excessive residual deformation of the shells on unreinforced areas (P ≤ σ po).
Fig. 3.70. Technological scheme of diffusion welding with low-intensity force action of structures of complex shape:
a is the required construction; b - billets for welding; c - welding; d - the nature of the deformation of the structural elements during welding; 1 - outer shell; 2 - inner shell
In a number of cases, it is possible to exclude the use of external pressure to compress welded workpieces using the phenomena of thermal stress arising when materials with different coefficients of linear expansion are heated. When welding coaxially-assembled blanks, the coefficient of linear expansion of the female part must be less than the coefficient of linear expansion of the male part (see Figure 3.66, a).
The quality of the joint during diffusion welding in vacuum is determined by a complex of technological parameters, the main ones being temperature, pressure, and holding time. The diffusion processes underlying the formation of the welded joint are thermally activated, so increasing the welding temperature stimulates their development. To reduce the compressive pressure and reduce the duration of welding, the heating temperature of the welded parts should be set as high as possible; metals have a lower resistance to plastic deformation. At the same time, it is necessary to take into account the possibility of the development of processes of structural transformation, heterodiffusion, the formation of eutectics and other processes that lead to a change in the physico-mechanical properties of the metals being welded.
The specific pressure affects the rate of formation of the diffusion bond and the amount of accumulated deformation of the welded workpieces. In most cases, the higher the specific pressure, the less welding time and more deformation. Thus, when welding in a press using high specific pressures (up to several tens of megapascals), the time of compound formation can be measured in seconds, and the deformation of metal in the bond zone by tens of percent. When welding using low specific pressures (tenths of a megapascal), the welding time can be calculated in hours, but the deformation of the blanks to be joined is a fraction of a percent. Thus, the task of choosing the specific pressure should be solved taking into account the type of structures, the technological scheme and the geometric dimensions of the blanks to be joined, and the welding time should be chosen taking into account the temperature and the specific pressure. When welding dissimilar materials, the increase in the duration of welding can be accompanied by a decrease mechanical characteristics compounds due to the development of heterodiffusion processes leading to the formation of brittle intermetallic phases in the junction zone.
To carry out diffusion welding, over 70 types of welding diffusion-vacuum plants have been created. The development and creation of diffusion welding systems is currently being carried out in the direction of unifying systems (vacuum, heating, pressure, control) and welding chambers. By changing the chamber in these installations, it is possible to significantly expand the range of welded assemblies. Some types of structures made by diffusion welding are shown in Fig. 3.71.
Fig. 3.71. Examples of titanium structures manufactured by diffusion welding
DIFFUSION WELDING
1. The essence of the method and the main applications
Diffusion welding is part of a group of methods for welding with pressure, in which the joint passes through the plastic deformation of the microroughness on the surface of the welded workpieces at a temperature below the melting point. A distinctive feature is the use of elevated temperatures with a relatively small permanent deformation. Its technological characteristics were proposed by N.F. Kazakov and accepted by the International Institute of Welding in the following formulation: "Diffusive welding of materials in the solid state is a method of obtaining an all-in-one compound formed as a result of the appearance of bonds at the atomic level that resulted from the approach of contact surfaces due to local plastic deformation at an elevated temperature providing mutual diffusion in the surface layers of the materials to be joined. "
In the practice of diffusion welding, it is known to use two process flow diagrams that differ in the nature of the application of the load or stress acting during the cycle. In one of them, a constant load is used at a value below the yield point. The processes developing in the welded materials are similar to creep. This technology is called diffusion welding according to the scheme of free deformation. In practice, such a scheme is feasible most simply, therefore it is very widespread.
According to another scheme, the load and plastic deformation are provided by a special device that moves during the welding process at a controlled rate (see Figure 1, b). This technology is called diffusion welding under the forced deformation scheme (DSPD process). This process is carried out at stresses, generally exceeding the yield strength. Thus, the strain rate £ is given by the applied load P and the conditions in which it acts: first of all by the temperature T and the action time 1.
Industrial application. The technological possibilities of diffusion welding make it possible to widely use this process in the instrument-making and electronics industries when creating metal-ceramic and cathode assemblies, vacuum-tight joints of dissimilar materials, semiconductor devices, in the production of stamps, etc.
Fig. 1 Scheme of deformation during diffusion welding:
1 - immersion system; 2 - deformation system;
Н - heater; D-parts
Diffusion welding finds application for the manufacture of large-sized blanks of complex shape parts, the preparation of which by machining, pressure or casting methods is impossible or uneconomical. Especially effective is the use of diffusion welding in experimental and small-scale production.
It is promising to obtain multilayer hollow structures, such as panels made of titanium or aluminum alloys with filler of complex shape (corrugated, honeycomb, rib, etc.) by combining diffusion welding and shaping in the superplasticity regime.
2. Basic parameters of the mode
When welding according to the scheme of free deformation, the main parameters of the process are the temperature of heating of the blanks T, 0 C; compressive pressure p, MPa; welding time t, min; the pressure in the vacuum chamber is pc. Pa; in the case of carrying out the process in another medium, the characteristic of this medium from the position of the course of oxidation-reduction reactions (type and chemical composition of the medium, dew point, partial pressure of oxygen). In addition, the important parameters of the process include the preparation of the surface for welding: surface cleanliness, its roughness and waviness.
In the DSPD process, the main parameters are: the temperature T, the growth rate of the load P, the deformation rate k, the deformation time t (or the degree of accumulated deformation), the holding time in the relaxation mode t rs. The resistance to deformation P in this case is the dependent parameter. Its value is recorded directly during the entire welding cycle. Both parameters can be used to control and control the quality of the connection.
Diffusive welding can be carried out in a vacuum, neutral and reducing gases, liquid media. Vacuum creates the best conditions for protecting the heated metal and cleaning the welded surfaces from contamination. However, in some cases, the material features may impose certain restrictions on the use of vacuum or make it completely impossible. In most cases, the diffusion welding process is carried out at a pressure in the vacuum chamber p k = 10 -2 ... 10 -3 Pa. The use of a higher vacuum is justified when it is necessary to ensure a high dimensional accuracy of the product (reduction of residual deformation of the workpieces) due to a corresponding decrease in temperature, pressure and time. Refractory metals can thus be welded at temperatures below the recrystallization threshold and thereby avoid embrittlement of the material.
The course of diffusion welding is significantly affected by the partial composition of the residual gases in the chamber. The entry of vacuum oil vapors into the working zone leads to an increase in the partial pressures of oxidizing gases (CO2, H 3 O) as compared with reduction gases (CO, H 2). Special measures (nitrogen traps, use of oil-free pumping means) improve the conditions for conducting diffusion welding, especially at low temperatures.
Widely used as protective media are inert (argon, helium) and active gases (hydrogen, less often carbon dioxide). The composition of the protective gas is selected primarily based on the chemical activity of the metal-gas system under welding conditions.
Preparing blanks in the general case can be composed of machining, cleaning from contamination and deposition of sublayers. Machining provides: perhaps a more dense initial fit of the welded workpieces; removal from the surface of the contaminated layer; increasing the dimensional accuracy of the finished product; the possibility of reducing the temperature, pressure and time of welding with the improvement of surface microgeometry.
With the increase of purity of processing, the development of the second stage of the process is facilitated.
Cleaning of surfaces from contamination (traces of fats, oil, polishing paste) can be carried out with solvents (acetone, alcohol, carbon tetrachloride, etc.), by heating and holding in a vacuum chamber. In some cases, annealing blanks in a hydrogen medium is used. Positive results are obtained when processing in solutions of acids H 2 S0 4, MCI, followed by washing and drying. When welding products from ceramics, after machining, the blanks are annealed to "heal" the surface defects. For this, etching of the glass in hydrofluoric acid is carried out.
To select the temperature, pressure and time there are no strict recommendations. High-quality connections can be obtained by changing within certain limits the values of each of these parameters with the appropriate correction of the others. When choosing their values, it is necessary to take into account the features of the materials to be welded and the requirements for the product; the possibility of softening due to grain growth, limitation of the heating temperature and deformation of the product, etc.
The welding temperature is usually set within (0.5 ... 0.8) Tm, for high-temperature alloys - slightly higher. When combining dissimilar materials, the calculation is carried out according to the melting point of the most fusible of them. In the case of a eutectic, the welding temperature is chosen to be below its melting point.
The heating and cooling rates depend on the source of heat and in most cases they are not regulated. When welding dissimilar combinations of materials, the thermal coefficient of linear expansion of which differs by more than 2 10 -6 deg -1, the cooling rate should be reduced to 10 ... 15 0 С / min.
It is recommended to conduct the decompression of the chamber when welding ferrous metal parts at a temperature of ≤120 ° C, and for colored and active metals at 60 ° C.
The holding time, depending on T and p, allowable residual deformation, the purity of contact surface treatment and the deformation capacity of the material, can vary from a few seconds to several hours (more often 5 ... 10 min).
The pressure is selected in the range 0.8 ... 0.9 of the yield strength at the welding temperature. For known structural materials, it can vary in the range 1 ... 50 MPa. For welding refractory and solid materials, these values can be several times higher.
4. Process technological capabilities
Diffusion welding allows you to weld:
Most of the construction materials on a metal base, ferrites, ceramics, glass, quartz, sapphire, graphite, semiconductor materials in homogeneous and heterogeneous combinations;
Porous, cermet, composite materials without disturbing their texture and deteriorating service properties;
When using the appropriate barrier coatings and spacers - heterogeneous metals and alloys prone to brittle phases, refractory metals (tungsten, niobium, tantalum, etc.) at temperatures below the recrystallization threshold.
Diffusion welding also makes it possible to avoid embrittlement of the metal. Using intermediate spacers, it is also possible to combine materials with sharply different values of thermal expansion coefficients.
Diffusion welding can be performed all types of joints in the most diverse design of their design: butt-end, stitch, connect the intersecting rod elements with each other and with flat or curved surfaces; weld blanks of any section; when using local heating and vacuum - to join blanks of unlimited length; to weld films, foil a few micrometers thick and sufficiently massive parts; To carry out welding at almost any thickness of the workpiece.
After diffusion welding, there is no need for mechanical processing of the welded seam, the resulting products have high dimensional accuracy (residual deformations in the range of 0.1 ... 6%); Seams have high mechanical strength and ductility at the level of the base material.
When using this method, good hygienic conditions are created in the production.
The disadvantages of the method include the considerable duration of the process, the complexity of the equipment, certain difficulties with the loading of blanks and the unloading of finished products from the working chamber in the organization of a continuous process of manufacturing welded products, the requirements for a sufficiently high accuracy of assembly and cleanliness of the surfaces to be welded, the need to control the temperature of the workpiece in the weld zone . High demands on the quality of contact surfaces increase the cost of the process as a whole.
5. Varieties of welding methods
Diffusion welding with intermediate gaskets. Intermediate gaskets may be melted and non-melting. The sublayers on the surfaces to be welded are applied in order to:
Increasing the strength of adhesion (welding);
Prevention of the appearance of undesirable phases in the welding of dissimilar materials (barrier sublayers);
Intensification stage volumetric interaction;
Facilitating the establishment of physical contact throughout the welded surface by using sub-layers of plastic materials;
Decrease in temperature and pressure during welding and, hence, reduction of residual deformations.
Depending on the specific task, the material of the sublayer is selected. Most often it is nickel, copper, silver, gold. The thickness of the sublayer is of the order of 2. ... 7 μm.
To prevent the appearance of undesirable phases (intermetallic compounds, carbides, etc.) or to avoid depletion of one of the welded materials by some alloying element, thicker coatings serve as a barrier. This task can also be performed with foil pads.
The material of the barrier gasket should be chosen so that its diffusion coefficient in the base material is higher than for the base metal elements in the gasket.
In the case of welding materials based on oxides (ceramics, glass), the applied metal layer is subjected to thermal treatment to oxidize it or facilitate diffusion into the workpiece material. When welding quartz glass with copper, a layer of copper is applied to the glass, followed by its oxidation at a temperature of 800 0 C for 3 ... 5 minutes to nitrous oxide. When welding copper with optical ceramics based on zinc sulphides, preliminary sulphidation of the metal is used to increase the adhesion strength.
As melting gaskets, high-temperature solders are most often used. Their use makes it possible to reduce the compression pressure and plastic deformation, facilitate the removal of oxide films, improve the performance of the joints.
Diffusion welding with impact loading. In order to prevent intermetallic compounds in the welded joint zone, in addition to the use of the respective intermediate gaskets, a noticeable reduction in the welding time is effective. In practice, this technique is realized by the so-called "shock welding in a vacuum". The essence of the method lies in the fact that a single impulse of force "applied" to the locally heated zones of contact of the component at a speed of 1 ... 30 m / s. In the parts to be welded under the influence of a dynamic load, local plastic deformation occurs in the contact zone and the formation of a welded joint. The welded joint is formed in 1 ... 10ms.
6. Equipment
The most widely used welding diffusion vacuum units. The composition of these units generally includes a working vacuum chamber, a mechanism for creating welding pressure, a heating source, a vacuum system, control and monitoring equipment. Specific installations (P-114, P-115, DF-101, USDV-630, DSV-901, UDS-ZM, etc.) for diffusion welding can have different design for individual functional units and systems.
The working vacuum chamber in which the welded article is placed, the heaters, the pressure mechanism, is usually cylindrical or rectangular in shape from corrosion-resistant steel. Walls are water-cooled. The product to be welded can be placed on a special support or in a fixture. In most cases, the installation has one camera. To increase productivity, several chambers can be provided in order to obtain continuous loading and unloading of blanks and products (lock chamber).
The required welding force is created by a hydraulic, pneumatic or mechanical device. In some cases, the compression of blanks is provided by special devices, the principle of which is based on the difference in coefficients of linear expansion of the materials of welded blanks and the components of the device that surround them. Such devices allow welding in commercially available vacuum and hydrogen furnaces. It is possible to use "soft" shells-cameras. Compression of blanks occurs due to the pressure drop of the external gaseous medium and the evacuated space. In most cases, hydraulic and mechanical systems are used in diffusion welding installations.
For induction heating, induction, radiation and contact methods are most widely used. The power source is high-frequency generators and transformers. Heating by high frequency current (HF) is the most universal and allows to heat billets in the diluted state (in contrast to the contact method), which is important for intensifying the process of cleaning the welded surfaces. However, this method is not applicable for the welding of dielectric materials: ceramics, quartz, glass. For heating, a glow discharge, defocused electron beam, light radiation is suitable.
More in the same section Industry, manufacture:
- Quality of production and organization of technical control
Diffusion welding is a type of soldering of metal billets, which is carried out under high temperature pressure by applying pressure to the parts with a squeezing vacuum. What this technique represents is discussed in more detail in this article.
Methods of application of diffusion welding
Diffusive welding can take place in two technological modes, which differ in the way the pressure is applied to the surface. The first method is to apply pressure to the welded part of a permanent nature, bringing the process to the limit of the melt.
Technology is widely applicable in connection with the free formation of products. The second way is to use special equipment that has a rotating shaft, which allows to create a load action on the part to the state of fluidity.
Advantages and disadvantages
Diffusion welding has such advantages:
minimum power consumption in comparison with other inverters;
electrode wires and solders are not used to connect the diffusion;
high rates of connection;
possibility to connect any geometric elements;
safe workflow.
To drawbacks include such features:
the welding diffusion process requires the presence of a vacuum unit, the absence of which makes the process impossible;
the need for preliminary stripping of the surface of the Bulgarian;
duration of the operating mode.
Welding methods
Diffusion welding is performed on the basis of gaskets having a melting and non-melting property. As the gaskets, nickel, copper, silver and gold alloys are used. A special sub-layer is applied to the weld zone, which is intended for:
improving the quality of the joint;
obstacle to the formation of porosity in metal fibers;
capturing a larger area of blanks;
contacting the surface of the welded element;
stabilization temperature conditions without destroying the inner layer.
Diffusion qualities can both have a positive effect on the weld seam, and negatively due to destructive temperature effects. To maintain a stable energy phase, a thick-walled foil can serve as a barrier. The main material is selected taking into account the diffuse coefficient, which should be higher than the index of the main billet. If glass or ceramic products need to be soldered, then the metal sublayer is heated up to an oxidizing reaction. This will help further the joining process, where diffusion will flow faster.
The soldering of copper products, which are characterized by oxidation, is carried out under the effect of a temperature of 800 ° C for 5 minutes. To connect ceramic and copper parts, zinc sulphide is used.
High temperature sources allow to reduce the compression process and make the process of eliminating the oxide coating easier. Thus, the operating time is significantly increased.
Diffusive welding by shock loading in vacuum is applicable in the case of the formation of metalloid pores in the weld zone. This method allows the contact area of the parts to become extremely hot, after which the action of a single force pulse occurs, the speed of which is 1-30 m / s.
When a dynamic load is applied to the surface of the blanks in the heat generation zone, a dynamic effect that facilitates the melting process takes place. Metal in the liquid state fills the connecting points and produces a smooth seam. This occurs in 1-10 ms.
Diffusion Welding Technology
Diffuse welding is used in practice in two ways: the first involves a constant supply of energy impulse to the workpiece element, the second technology consists of a combined connection, which is based on plastic deformation and compression force. Speed mode is adjustable during welding.
Diffusive welding consists of this kind of sequence: first, the harvesting parts of the equipment are collected, which allows you to apply the necessary load to the connection zone. Further, the parts are vacuum-treated so that they are easier to heat. After the exposure to the metal has ceased, the product must remain at rest until completely natural cooling occurs.
Education welding seam is produced in two ways: physical and formation stages. The first method is carried out by means of physical pressure on the weld zone. The second method involves warm-up, pressure, compression.
Time mode can be set depending on the density of the welded part. It can vary from a couple to several tens of minutes. The melting of the metal fibers occurs by induction, and the process can be affected by an electric beam having an inverse resistance. The connection occurs in a non-oxidative heating mode. For the protective function of oxides, vacuum is used, and the initial parts are thoroughly processed before the action.
Page 1
Vacuum welding provides non-oxidizing heating and is used to connect the critical parts of instruments and measuring instruments, for example, for joining carbide-tipped plates to steel in the manufacture of end-length measures reinforced with a hard alloy.
For vacuum welding parts of small thickness are collected tightly, without visible gaps IB joints, and not on press fit.
An interesting method of vacuum welding with a consumable electrode, developed recently in the MVTU - MEI. With this method of welding, arc combustion occurs in metal vapor. The method is very rational for welding thick-walled products from aluminum, titanium and other alloys. Welding in vacuum with a consumable electrode is efficient, the heating is obtained concentrated, the quality of the connections is high. At present, large-sized welding chambers for this method have already been developed.
One of the types of vacuum welding is diffusion. In this method, the vacuuming, heating and compression of the parts are successfully combined. When vacuum welding, the heating temperature is much lower than the melting point. This makes it possible to carry out joints without negative thermal influence on the metals adjacent to the seam. Diffusion welding combines various homogeneous and dissimilar refractory metals, alloys, oxides, ceramics. At the present time, various developments and studies are being carried out to improve the equipment for diffusion welding and technological processes of joining all kinds of materials.
Electrodes suitable for vacuum welding should provide a weld metal having a high plasticity, very dense, not prone to cracking, with easily detachable slag crust.
In France, a method of vacuum welding of refractory and chemically active metals by an electron beam has been developed. In this method, the surface of the metal in a vacuum melts due to the energy given off by bombarding electrons upon impacts on this surface. By directing a beam of electrons to the welding site, the metal of the welded parts is melted here.
The thickness range of parts welded by diffusion vacuum welding is very large.
In particularly critical cases (in vacuum welding, etc.), it is advisable to remove the surface layer of copper to a depth of 0.4-0.5 mm.
Most of this book focuses on vacuum welding and soldering, which is of particular importance in vacuum instrumentation.
For refractory and highly active metals, vacuum welding with an electron beam can find application. This method has not been developed yet, implementation of it meets some difficulties, but, undoubtedly, it opens the possibility of combining some difficult-to-digest materials. To increase the productivity of welding with an electron beam, it is necessary to introduce automated and mechanized processes in production, ensuring the continuous operation of the installation.
With respect to the supply of oxygen, no special requirements for vacuum welding are also required.
Nitrogen is cheap, but can not be used for vacuum welding of steel, because at high temperatures in the nitrogen environment, iron and chromium nitrides are formed, which have very high hardness and make weld seam uneven and porous.
The conditions for obtaining 1 vacuum-dense welded and soldered joints are specified, briefly described best practices vacuum welding and equipment for it. Formulation and methods of flux preparation for vacuum soldering of ferrous and non-ferrous metals are given.
FEDERAL AGENCY FOR EDUCATION
STATE EDUCATIONAL INSTITUTION
OF HIGHER PROFESSIONAL EDUCATION
Moscow State Institute of Radio Engineering, Electronics and Automation (TECHNICAL UNIVERSITY)
COURSE WORK
"MODEL TECHNOLOGICAL PROCESS
DIFFUSION WELDING IN VACUUM »
Completed student gr. ES-11-06
Ivleva Yu. I.
Teacher
Rybnikov Yu.S.
Moscow 2009
Introduction .............................................................................. ... page 3
Technological route map ............. ................................. .p.5
Characteristic and technical requirements to the raw materials ...... page 5
Typical technological process ................................................ page 5
Equipment, rigging and tools ....................................... ... page 5
Quality control ..................................................................... page 5
Safety and industrial sanitation requirements ............ page 6
Annex 1, Fig. 1 ................... ................................................ page 7
Introduction.
Diffusion welding is widely used in engineering. A distinctive feature is the use of relatively high heating temperatures and comparatively low specific compressive pressures with isothermal exposure from several minutes to several hours.
The formation of the diffusion bond is determined by such processes as the interaction of the heated metal with the gases of the environment, the cleaning of the welded surfaces from oxides, the development of high-temperature creep and recrystallization.
To reduce the rate of oxidation of welded workpieces and create conditions for cleaning contact surfaces from oxides during welding, gases can be used - reducing agents, salt melts, fluxes, coatings, more often vacuum or inert gases.
Approximation of welded surfaces occurs due to plastic deformation of microprotrusions and surface layers caused by application of external compressive stresses and heating of the metal.
In the process of deformation of the surfaces to be welded, their activation takes place, and when they develop physical contact between them, their setting is realized.
In the case of diffusion welding of like metals, the welded joint achieves an even strength of the base material and when the structure of the bond zone does not differ from the structure of the base material. To do this, common in the contact zone for the joined grain. This is possible due to migration of the grain boundaries, either by recrystallization of the treatment, or by collective recrystallization.
The joining blanks can be quite different in shape and have compact or developed contacting surfaces. The geometric dimensions of the parts to be welded are in the range of several microns to several meters.
Diffusion welding - The method of welding without melting the base metal by heating and squeezing the parts to be joined. In the place of welding of parts, diffusion of one metal into another takes place. Parts with carefully cleaned and fitted surfaces are placed in a closed welding chamber with a vacuum of ~ 0.01-0.001 n / m 2 , that is, up to 10 -5 mm gt; art. . The parts are squeezed with a small constant force, to increase ductility and accelerate the diffusion, heat up to 600-800 ° C. When heated in a vacuum chamber, intensive cleaning of surfaces from organic contaminants and oxides occurs. In some cases, after depressurization, the article is additionally maintained at the welding temperature for a more complete flow of recrystallization processes that contribute to the formation of a qualitative compound. A few minutes after the end of welding, the parts are cooled in a vacuum, inert atmosphere or in the air, depending on the type of equipment.
Depending on the stresses that cause deformation of the metal in the contact zone and determine the process of formation of the diffusion bond, welding with high-intensity and low-intensity force is distinguished. In the first case, the welding pressure is created by means of a press equipped with a vacuum chamber and a heating device. But such installations allow to weld details of the limited sizes (to 80 mm).
To exclude the possibility of loss of stability of welded elements, transfer of pressure to the welding zone and creation of conditions for locally directed deformation of the weld metal in the joint zone, diffusion welding is carried out in devices using technological insets and blocks to fill intercostal spaces, which are removed by chemical treatment or dismantled after welding.
The quality of the connection depends on the temperature, pressure and holding time.
The diffusion processes that form the weld joint are thermally activated, so increasing the welding temperature stimulates their development.
When welding dissimilar materials, the increase in the duration of welding can be accompanied by a decrease in the mechanical characteristics of the joint due to the development of heterodiffusion processes.
Currently, over 70 types of welding diffusion-vacuum plants have been created, changing the chamber in these installations, it is possible to significantly expand the range of welded units.
Parameters of diffusion welding process technology:
- welding temperature up to 0.7-0.8 T melting;
- specific compression force up to 1-2 kgf / mm 2;
- the time of heating the parts to the welding temperature;
- cooling time of the product;
- the degree of vacuum in the vacuum chamber is from 0.1 to 5 · 10 -3 mm Hg
Advantages of the welding process:
- the possibility of obtaining compounds of homogeneous and dissimilar materials;
- small deformations of welded parts (5-7%);
- non-waste technology;
- environmentally friendly process of machines for diffusion welding;
- there are no consumables (expensive solders, fluxes, pastes);
- the possibility of obtaining a connection with a large area of the weld zone (limited by the force of the compression drive unit);
- the only reliable way to get flexible copper buses, connections, compensators by soldering the places for bolted connection;
- replacement of soldering for diffusion welding saves expensive brazing alloys, significantly improves the quality of joints: provides stable electrical contact, no contact resistance of the joint, strength, thermal and corrosion resistance increases, the appearance of the product is flawless, there is no scale and traces of rustiness;
- diffusion welding of copper with silver and nickel foil replaces galvanic coatings
Areas of use:
- products of low-voltage and high-voltage equipment (for example, contactors electromagnetic, disconnectors, oil, vacuum and automatic switches; contacts; starters; complete transformer substations for package transformer substations; high-voltage CSR cameras for switchgears and switchgears KRU, etc.);
- busbars, flexible buses, connections, expansion joints, current leads;
- termination of wires and cables (replacement of cable lugs);
- composite materials with specified properties;
- the elements downhole pumps (bimetallic saddle and valve stem);
- transformers and electric machines.
Technological route map.
The present typical technological process describes the formation of a diffusion connection of homogeneous materials and equipment and equipment for its implementation.
1. Characteristics and technical requirements for the raw materials.
1.1. A distinctive feature of diffusion welding from other methods of pressure welding is the relatively high heating temperatures (0.5-0.7 Tm) and comparatively low specific compressive pressures (0.5-0 MPa) with isothermal exposure from several minutes to several hours.
2. Typical technological process of welding homogeneous materials from copper.
2.0. The technological scheme of diffusion welding is given in Appendix 1.
2.1. Sequence of the technological process:
2.1.1. Preliminary preparation surface:
1. degreasing with trichlorethylene;
2. washing with hot and distilled water;
2.1.2. Installation of manually welded parts in a vacuum chamber, closing the door of the camera.
2.1.3. Pumping air from the chamber.
2.1.4. Approximation of welded surfaces.
2.1.5. Heating the parts to the welding temperature ≈600-800 ˚С
2.1.6. Compression pressures of 1-2 kgf / mm² for a given time period of 3-15 minutes.
2.1.7. Cooling of the compound in a vacuum.
2.1.8. Air in the chamber.
3. Equipment, rigging and tools.
3.1. Specialized installations and diffusion welding machines consist of a power source; vacuum and electrical systems; cooling systems vacuum chamber, welded parts and electrodes; compression force drive; hydraulic or pneumatic compression force drive system. Electrocontact heating of parts during welding is carried out by alternating or direct current. The plant control system is based on relay or microprocessor technology.
4. Quality control.
4.1. Definition of visual conformity to appearance. 4.2. Determination of the strength of the seam to break with a tearing machine. 4.3. Determination of the vacuum density (tightness) of a helium leak detector.
5. Safety requirements and industrial sanitation.
5.1. When working with specialized installations and vacuum furnaces of diffusion welding, it is necessary to be guided by the following normative materials:
A) / "Production buildings industrial enterprises. Design standards »/ SNiP, P-M, 2-74 /; B) / "Fire prevention requirements. Basic design provisions »/ SNiP, П-Е, 7-74 /; B) / "Heating, ventilation and air conditioning. Design standards »/ SNiP, П-Е, 7-74 /; D) / "Internal water supply of production and auxiliary buildings of industrial enterprises. Design standards »/ SNiP, PG, 2-74 /.
5.2. Safety measures during operation and maintenance line. 5.2.1. Operation of presses working under pressure is allowed to personnel who have certificates of passage of the "Rules for the operation of pressure presses". 5.2.2. All line equipment must be properly grounded and regularly checked during operation. 5.2.3. It is forbidden to be in the zone of vacuum and electrical systems without safety clothing, glasses, a respirator. 5.2.4. Before starting up the machines, each time it is necessary to check the operation of the vacuum chamber cooling system, welded parts and electrodes, drive compression force, hydraulic and pneumonic compression system. 5.2.5. Before the remote control must be dielectric mats. 5.2.6. When the system is operating, control cabinet cabinets must be closed with a key. 5.2.7. The electrical system must be switched off when the machines are not working. 5.2.8. When working with a triboelectric charger, the generated d.C. must be taken to the ground.
Annex 1.
Technological scheme of diffusion welding: a - the required design; b - billets for welding; в - assembly; r - welding; d - finished structure; 1 - supporting sheathing; 2 - finished aggregate; 3 - technological sheets; 4 - membrane.
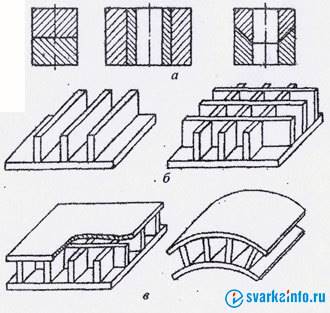
Fig.1. Some types of structures obtained by diffusion welding.