Electrodes for welding with direct current. What electrodes to choose for welding products inverter.
We will discuss how to choose electrodes for manual arc welding, pay attention to the classification of electrodes and their marking.
The electrode is a metal rod for supplying current to the work piece. During welding, the edges of the welded parts are melted and the metal is filled with the electrode. This type of welding is also called welding with coated electrodes, since the electrode is coated with a layer of flux, which, when melted, forms a gas shield for the weld.
The thickness of the parts being welded oversteps the diameter of the electrode. Therefore, first determine the required electrode diameter.
For welding thicknesses up to 1 mm in Europe, use electrodes with a diameter of 1.6 mm (for real professionals), in Russia they can only be found on the order. As a rule, in this case the method of manual arc welding is not applied, but using welding with argon or semiautomatic device.
If you want to get a reliable and beautiful seam with minimal effort, then first of all buy good electrodes! Choose electrodes for manual welding (they are also called disposable electrodes) in accordance with the chemical composition of the parts to be welded.
Electrodes can be divided into several conditional groups:
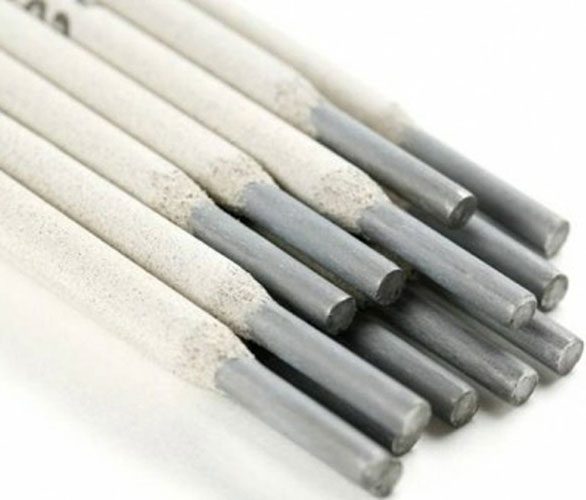
- by diameter (2-6 mm);
- by marking;
- by manufacturer.
Electrode marks
Consider only the most popular marking and analogues of electrodes.
SSSI— electrodes for direct current with the main coating. For responsible structures of all kinds of steel.
OZS— rutile electrodes, universal, for work both on permanent and alternating current. Compared with SSSIs require less welding current and form less slag.
MP3 - electrodes also with rutile coating, for welding with alternating and direct current.
ANO-4 is another popular universal electrode. Most often they are sold in small packages of 1 kg, which is very convenient. And if at the dacha you suddenly needed something to grab and for this you need 2-3 electrodes, then you will not have to buy a large pack of 5-6 kg, which can then be damped while it is stored, but this small one is enough. Convenient and economical.
TSU-5 - specialized electrodes for welding pipes(water supply).
ESAB OK 53.70 - coated electrodes for welding water pipes, analogue TSU-5.
ЦЧ-4 - electrodes for cast iron.
ESAB OK 92.18 - for cast iron, an analog of the TCH-4.
ЦЛ-11 - for welding stainless steel.
ESAB OK 61.30 - stainless steel electrodes, an analog of TL-11.
ESAB OK 96.20 - electrodes for welding aluminum.
KOBELKO LB-52U - popular Japanese electrodes, for critical structures. Can be used even for welding of water and gas pipes. The best and most expensive.
Manufacturers of electrodes
Let's talk about the manufacturers of electrodes, as this is most often reflected in their quality.
KOBELCO - Japan. The best electrodes , but also the most expensive. Excellent results when tested for strength.
ESAB - electrodes ESABhigh Quality. Most often in shops you will find these electrodes at a rather high price. But! These electrodes are really worth it.
"Losinoostrovsky factory" - electrodes, average for price and quality.
Kamenskiy Zavod - reliable electrodes with good ratio price and quality.
"Ural Plant" - most often these are the cheapest electrodes. Do not expect excellent quality from them. In general, they will weld and keep the construction.
Storage of electrodes
Store the electrodes only in prepared areas. When buying, pay attention to the expiration date. Overdue electrodes will not give comfortable welding and reliable connection of parts!
Store the electrodes better in a special pencil case, which will prevent moisture from entering. The pencil case also serves to transport the electrodes to the welding site. If the electrodes are still damp, then drying the electrodes and calcining the electrodes will help. To do this, use baking oven , which heats up to 400 ℃. If you put the electrodes in the pencil case still hot, after heating in the oven, it will keep the heat for a long time.
The review of the best electrodes for manual welding of carbonaceous and corrosion-resistant steels is made using the publications of the magazines "Welding and Diagnostics", "Metallurgical Bulletin" and other specialized sources. The article summarizes the online reviews of professional welders about the products of different manufacturers.
Selection criteria
Unfortunately, Russian electrodes lose to many foreign analogues in most parameters. However, "breakthroughs" in this area have already been outlined. The Russian electrode products, produced at a few joint ventures, are no worse than many venerable brands in terms of quality stability. Some factories of domestic subordination also began to "pull" to them. However, in cases where it is required to ensure a high quality of the seam confidently, professionals still prefer to use more expensive, but also better quality foreign electrodes. For welding inverters Electrodes of any type are suitable, not all types are suitable for AC welding machines.
When choosing the best electrodes for review, we were guided by the following criteria:
- production volumes;
- product quality;
- hit the manufacturer in the reviews of the electrode industry;
- reviews of professionals.
For the correct comparison of prices, we included in the review only the most commonly used electrodes with a diameter of 3 mm.
The main parameter of any welding electrode, determining the majority of its properties - from the ease of ignition to the quality of the seam - is the composition of its coating. The most common today are the following types of shaving:
- Rutile electrodes (and electrodes with mixed coating on this basis - rutile-cellulose, etc.) have become one of the most popular due to the ease of ignition, including repeated, reduced (within reasonable limits) sensitivity to depletion. They can be used for both alternating and direct current in all directions of the seam, but when choosing the rutile electrode one needs to be careful - you can buy both a good electrode and a contaminating seam with a huge number of slag ulcers, which is suitable only for stitches.
- Electrodes with basic coating most often used in welding direct current in particularly responsible places. When the coating is burned in large quantities, carbon dioxide, reliably protects the welding bath from the effects of oxygen. The seam itself is more plastic than in the welding of common types of rutile electrodes. The reverse side of the coin is the increased sensitivity to humidity and the difficult ignition: it is much more difficult to cook with such electrodes.
Many are interested in the question of which electrodes for inverter welding are recommended by professional welding professionals, since it is the inverter that is often used by domestic craftsmen.
1 What is inverter welding?
Welding inverters have long ago supplanted the standard transformer units used previously. This is due to the fact that an inexpensive and easy-to-use inverter makes it possible to weld any metal constructions and details.
As a rule, such apparatuses are used in the arc welding process by melting as highly reliable power supplies. Inverters are characterized by a constant index and stability of the welding current, which guarantees the production of an ultra-strong connection of materials due to the excellent quality of the obtained seam.
Inverter welding is generally understood as a process involving the use of a special unit capable of generating an alternating voltage when the power source is turned on. In the welding operation with the help of an inverter apparatus, "other" devices included in the welding scheme also "participate":
- control system;
- network rectifier and filter;
- transformer (high-frequency);
- frequency converter.
Well, the main tools for inverter welding are, of course, different. They are metal electroconductive rods, required for supply to the welding zone of the current. Here it is worth considering that different types of welding units (even completely of the same type) use different electrodes. Therefore, the selection of such rods, supplying current, should be done correctly.
2 The best electrodes for inverter welding - what are they?
Electrodes of a melting type, used for inverter and in general arc welding, are produced from a welding wire meeting the requirements of the 1970 State Standard 2246. According to this GOST, all welding electrodes with the use of an inverter unit are divided into:
- alloyed: made of wire Sv-08X3G2SM, Sv-08GSMT, Sv-10X5M, Sv-08GS, Sv-08HGSMA, Sv-08HN2GMTA, Sv-15GSTUTSA, Sv-06H3, Sv-08HNM, Sv-08HG2S, Sv-08G2S, SV -08ХГСМФА and others;
- carbon: from the wire Sv-10G2, S-08HA, Sv-08, Sv-10GA, Sv-08AA, Sv-08A and Sv-08GA;
- high-alloyed: from the wire Sv-30Kh15N35V3B3T, Sv-10Kh20N15, Sv-12Kh13, Sv-30Kh25N16G7, Sv-04Kh19N9S2, Sv-10Kh11NVMF, Sv-06Kh20N11M3TB, Sv-08H50, Sv-07X25N13, Sv-12Kh11NMF, Sv-04Kh19N11M3, Sv- 01Х23Н28М3Д3Т, Sv-10Х17Т and many others.
The rod of the electrode (on the surface) is coated by the method of crimping. Such a coating, first, protects the welding bath from the atmospheric influences, and secondly, it allows the arc to burn more steadily.
Novel welders using an inverter should know that all the electrodes are divided into two groups. The first includes products that are designed to connect the responsible metal structures, the second - the usual. Experts advise choosing electrodes of SSSI for welding of critical products and ANO or MR-3 for welding conventional ones. Note - the brand of SSSI electrodes is considered very "capricious". With such rods, not every novice worker can work, having no real experience in performing welding activities.
Now the most popular brands of electrodes for inverters are the following products:
- SSSI-13/55: in demand among experienced welders. These welding rods make it possible to obtain a really good weld (including low ambient temperatures) with an optimal density index.
- МР-3С: they are used at high requirements, put forward to the seam, for connecting parts with alternating and direct current of reverse polarity.
- MR-3: perhaps the most universal brand of rods. With their help, it is possible to weld metal with a contaminated surface, as well as wet and rusty structures.
- ANO: without a doubt, the electrodes most purchased in Russia. They do not require pre-baking, they ignite without any effort and guarantee an excellent result of the welding work (even when welding is performed by the person who first took the welding machine into his hands).
All these welding rods, sold through trade networks with epidemiological certificates, guarantee a 100% quality welding. In this case, the person using the inverter unit will work in the safest conditions.
In principle, the inverter is a modern unit that can boil a variety of surfaces with virtually all existing types of electrodes. This is his high popularity. But not all rods are capable of providing a truly qualitative welding result and a good marketable appearance of the seam obtained. And security issues when using electrodes that are not recommended for inverter welding, will frankly "limp". Proceeding from this, we conclude that it is really necessary to use the above-mentioned rods while operating the inverter.
At once we will add - at purchase of electrodes it is necessary to make sure of their authenticity (certificates of quality, licenses of the manufacturer), and also that products were transported, stored and packed in appropriate conditions. Only in this way can you be completely sure of their worthy quality and effectiveness of application.
4 Resanta - a well-known brand of inverters in the Russian market
Among the professional welders and domestic craftsmen, the inverters of the recognizable electrical brand "Resanta" are in high demand, the electrodes for inverter welding with the use of the units of this company are selected according to the scheme described earlier. You can safely purchase those brands of rods that we recommended to you. They are ideal for welding installations of "Resant".
Among the most popular inverter units of this brand are the following highly functional devices:
- series "Prof": functions "Fast and Furious Arc", "Hot Start", "Anti-stick", protection from overheating of the welding machine, wide interval of current control for welding process;
- series "Compact": the best option for home use;
- plasma inverter cutters "IPR-40" and "IPR-25".
Quality electrodes and reliable equipment are the guarantee of efficiency of welding operations.
Arc welding is performed using a transformer or. The second option is more popular in everyday life, due to its compact size and low weight. Any of these units works by means of electrodes.
The basis is a metal rod. Depending on, it can be:
Melting. It is made of steel electrode wire or special alloy. A special paste is applied over the metal rod - coating (coating).
The composition of the coating includes various chemical elements and additives, through which the correct configuration is formed welding seam. In addition, thanks to the coating, stable welding of the welding arc is maintained.
Non-melting. Electrodes of this type do not participate in the formation of a seam, but serve only as a source for the emergence of a welding arc. Are made of refractory materials. The most common is a tungsten rod.
Himself non-consumable electrode (based on the name) remains intact during the works. To form a weld in the melt zone, a filler material is supplied, in the form of a wire of the same metal as the billet.
Tungsten rods are used for aluminum welding inverter. Work is carried out in a neutral gas environment, for example - argon.
Both options considered refer to piece electrodes, that is, each of them is a separate element of a certain length. There are also continuous-discharge electrodes - the so-called welding wire.
It is fed into the area of contact with the workpiece, mechanically. The seam is formed due to its melting and flowing into the bath. Since the wire is a conductor - it provides the work of the welding arc. Cover for such an electrode is not provided, so all the elements to create correct seam are incorporated in the alloy.
To saturate the welding zone with the necessary additives and chemical elements, a flux-cored wire is created, which is a thin tube with the required composition in the middle.
Such wire is used in welding machines for inverter welding of the "semi-automatic" type. The electrode in the form of a wire (monolithic, or filled with powder) is inside and fed into the weld zone automatically, the operator only gives the command to turn on.
How the inverter works
To obtain a large value of the welding current, a large-sized transformer is required. It is inconvenient for transportation and maintenance. Unlike a welding transformer, the inverter works like a high-power switching power unit.
Transformation aC voltage at the input to the direct current of the desired value at the output occurs in several stages:
- the alternating current of 50 Hz with a voltage of 220 volts is rectified;
- the DC current is converted (inverted) to an alternating high-frequency one;
- voltage is reduced by means of a compact high-frequency transformer;
- rectifies the alternating current and is applied to the output terminals of the inverter.
In this case, the value of the secondary rectified current is high enough to perform any welding work.
The inverter circuit is built on powerful transistors operating on direct current. A transformer operating at a high frequency (60-80 Hz) takes up several times less space, and accordingly has a lower mass compared to a conventional welding machine.
Due to the applied circuit, with the same operating current strength, inverters have the size and weight, allowing the device to be carried by one operator, which is especially important when working at different heights.
Many welders of the old school, accustomed to working on welding transformers the size of a washing machine, accuse inverters of permanent sticking of the core.
These statements are unfair. Professionals who can work on any equipment know why the electrode sticks when welding with an inverter. The reason is in the wet coating. After 5-10 attempts, the coating from the high short circuit temperature dries, and the arc is perfectly lit.
IMPORTANT! Regardless of the type welding machine, the electrodes must be dry.
The coating has a porous structure, and absorbs moisture well. If you use electrodes from a long-opened bundle - they must be burned before starting work.
If you know how to properly cook - it remains only to pick up the electrodes by designation on the package. There are no special consumables for such welding machines. Welding electrodes for the inverter are no different from any others.
Therefore, when selecting consumables for welding, one must be guided only by the conditions of their application. It is enough for you to have information about the current produced by the inverter, the location of the seam and the name of the metal with which you will work.
How to boil the electrodes with an inverter, the correct selection of consumables
For domestic use, complex welding is not used. As a rule, as raw materials, simple materials - steel pipe, profile or corner. Often the car body sheet is restored. Sometimes it is necessary to cook stainless steel - for example, during repair washing machine or a pitted pan.
The composition of the core of the piece electrode is selected according to the type of metal from which the blank is made. That is, from structural steels and alloys based on them. For most household work, you do not need to have an assortment of dozens of electrode types. It is enough to remember 3-4 brands, which are considered universal and perfectly suited for beginners.
Professionals recommend these beginners to these welders, as they have average characteristics and do not require special conditions for work. In addition, the proposed brands are seamlessly compatible with all types.
Rutile electrodes MP-3
Ask any welder, from which consumables he started training - and you will get the answer: "MR-3". This brand is ideal for a beginner. The ignition occurs instantly, even if you are a little mistaken with the settings of the inverter parameters.
The bath is protected with additives from the coating, no special effort is required to control its position. If you can not "catch the arc" from the first time - just burn the electrodes at a temperature of 160 ° -190 ° 30-50 minutes. You can cook at any position of the welding seam, except for the vertical top-down.
Despite the versatility of the current (you can cook as a variable, and a constant) - the best seam is obtained on the inverters with a constant current.
The surface quality does not matter, corrosion or humidity on the surface is not a hindrance. If the first time you picked up the electrode holder, it should be MP3.
Basic SSSI Coating 13/55
The most common consumables are welder. Manufacturers recommend them for working on metals with a high carbon content. A sturdy seam resists shock loads well and has a high tensile strength. In Russia, these electrodes are also popular because seams tolerate low temperatures well.
SSSI 13/55 operate on direct current with reverse polarity, full compatibility with inverters.
Excellent seam characteristics are somewhat overshadowed by imperfections in use. For ignition of the arc, the idling voltage must be at least 65-70 volts. Electrodes are poorly brewed on a dirty and unprepared surface. Before starting work, the place of welding must be carefully cleaned.
Rutile electrodes ANO-21
A popular brand of tinsmiths from car service. The best consumable for working on thin steels with a high carbon content is not found. The arc is fired instantly, thin metal It is protected from through burn-through, and the seam turns out to be finely scaly. Accordingly, careful after-welding treatment is not required.
The second most popular field of application is welding of thin-walled pipes. This brand is well known to plumbers and gasmakers.
They operate on both AC and DC, which is suitable for inverters. Before use, it is necessary to calcine at a temperature of 120 ° -130 ° for an hour.
Working with stainless steel - OK 63.34
For the welding of stainless steel products, OK OK 63.34 is suitable. This kind of metal can be cooked with other electrodes, only the quality of the seam will be disgusting, and it will rust. These rods form a smooth seam with a fine-grained surface. The conjugation with the main surface is smooth, the seam is not corroded.
There are no requirements for the type of current, no-load voltage for ignition of the arc is not less than 60 volts.
Surfacing of metal
This type of welding work is used, if necessary, to repair a worn out part or a broken hole.
For surfacing requires special skills, so that beginners for this work should not be taken.
To restore the volume of metal, special electrodes will be required for surfacing the steel. This is a whole group of brands, in the name of which there is a letter "N". For example - TSNIIN-4 or OMG-N.
These brands are distinguished by a number of parameters, such as the deposition rate or the position of the seam. But all of them provide a qualitative increase in the thickness of the billet without loss of strength of the metal.
IMPORTANT! A novice welder should remember the main truth: It is not important how to boil aluminum or steel, the main thing is to know what to do.
In conclusion, a video on how to properly cook the inverter and what electrodes to use for welding. Case study on examples.
- Practical recommendations
- Electrode coating
- Additional points
The choice of welding electrodes is an integral part of such processes. Modern construction rarely does without the use of this type of work. And this applies to low-rise buildings (private and country houses) and to the construction of large commercial buildings.
The quality of welding, first of all, depends on the quality of the electrode with which the work was done, so it is necessary to approach it carefully and responsibly.
Frameworks, tanks, bases for garages and canopies, roof elements - all metal parts of these structures are connected together by means of welding. In order for the seam to be of high quality, reliable and durable, it is necessary to have good equipment and consumables. Therefore, the choice of the electrodes for welding is one of the main ones in the preparation of work. The quality of the welded joint depends on how well the electrodes are selected.
Equipment for welding works
There are several ways in which welding is performed:
- gas press;
- contact;
- roller;
- electric stepping.
But the gas-press and contact are isolated. When gas welding, the flame of acetylsilox is used. This method is chosen if it is necessary to achieve high productivity of the performed work. Therefore, industries where gas-welding welding is used are oil and gas when laying trunk pipelines for long distances.
When contact welding, the process is performed using electric current, which has low voltage and high current intensity. This method is performed manually or mechanically. In this case, the contact welding can be made butt-end, overlapping, the parts can be applied to each other at any angle. From the way the seam is adopted, the choice depends necessary equipment. As a result, the quality of the work depends on the choice of the electrode, the welding units.
The choice of welding equipment should be approached from the specific conditions of work. Namely:
The supply voltage of the welding machine for household use is 220 V.
- Supply mains voltage. Under production conditions it is 380 V, in domestic - 220 V. With frequent voltage surges, it is more rational to use an inverter that can protect the device from such influences and ensure reliable operation.
- Types and brands of metals that need to be combined. Constant current, which is required for welding parts made of cast iron or non-ferrous metal can provide a welding generator or rectifier. The transformer is used for welding elements made of ferrous metal.
- Weight of the welding machine. Not always a lot of weight indicates the duration of full use. Modern welding units, having a rather small weight, can serve for a long time, performing all the tasks set, in contrast to heavy obsolete models. This is especially true when there is a need for frequent movement both between objects and within the construction object.
- Operating time without possible overheating. This passport characteristic, which is indicated in the documentation for the equipment, indicates how long the machine can work without interruption to avoid the threat of overheating. For example, if the figures are 5x20%, it means the possibility of continuous operation for 1 minute, and then a break of 4 minutes is necessary.
- Output characteristics of the welding machine. At lower values of the output characteristics of current and voltage, it is possible to perform work with a thick metal. However, in such apparatuses, the winding is heated faster, therefore, the thermostat can cause the welding unit to be disconnected more quickly.
In addition to the welding equipment in the process of welding two or more metal parts involved electrode. To choice, which must be approached responsibly. It depends not only on the quality and durability of the seam, but also on the amount of weld metal and its composition.
Back to contents
The manufacturer of welding equipment often gives advice on which brands and types of electrodes can be used in combination with it. The wire that underlies the electrode must be of high quality initially. Further, the determining parameter of using a particular type of electrodes is its coating.
The choice of electrodes must be made based on the parameters and characteristics of the surfaces to be welded. It should be borne in mind that each of the brands of electrodes has its own peculiarities of application. If you use the wrong type of electrode, then weld seam can not work out.
Electrodes, according to normative documents, can be divided into several parameters:
- purpose of use;
- the type of coating and its thickness;
- mechanical properties and coating composition.
Back to contents
Electrode coating
The wire coating can be:
- Rutilov. It is made of titanium dioxide, which is used to spray onto the wire in the form of a powder. The use of this coating makes it possible to obtain a quality welded seam. Such electrodes contribute to stabilization in combustion. This grade is used for joining rusty or damp parts. A small amount of splashes formed during welding, contributes to a low consumption of metal during the work, the seam is neat. They are able to work both with the use of equipment operating on a constant or alternating current. Their cost is quite high, but the breadth of application of this type is fully justified.
- Ilmenitov. When the wire is coated, iron is added to the titanium dioxide. At work, a strong elastic seam is formed.
- Basic.
Carbonate and fluoride compounds are used as coating materials.
They are resistant to changing ambient temperatures. But a significant disadvantage of this type of electrodes is that their use is limited only to parts that do not have a rusty edge. However, they can be used when performing work in any position and direction (from top to bottom, from bottom to top). They are used for welding structures, which will later be operated at a low temperature with variable or shock loads. A feature of using these electrodes is that they can only be used in welding works, which are conducted by a constant current of reverse polarity.
In addition, there are still rutile-base and rutile-cellulose coatings. The electrodes, which are covered with the first one, are used for laying pipelines of any medium or small diameter. The second coating is applied to a wire to be used for welding a thick coating.