How to cook thin metal 0.5 mm by electric welding. Which electrodes are better for welding tins, thin metal
It happens so you need to brew a thin tin and you do not know which electrode you can cook it all. It is necessary to weld manual arc welding since the other one does not. You can use different devices, but the fact remains and it is clear that the electrodes tend to burn the tin. For the beginning take the electrode of the smallest diameter, it's a two or three. Then we look at the device.
You can cook as change and direct current . It is desirable to use generic electrodes. I would advise you grade c grade МР-3С blue . Why it was so customary and I welded them with thin metal. Metal can be superimposed in the overlap (on each other) is not much, and thus we have more chances that we will not burn it. Usually, this method is not suitable because you often need to connect products to the joint. What to do? Neither of which it is not necessary to be wise and we will use the same grade as an additional metal for welding. We clean it from powder spraying and apply it to the welding spot. It is there where the seam will pass.
If you are going to cook car tin then here the story is not much different. It usually leads from through the measured heating. And cook it with either a semi-automatic or other welding. Electrodes You can cook, but not all parts of the car. Suppose we have prepared everything you need:
- The electrodes are C grade.
- Prepared the parts before welding (cleaned the place of welding).
- We have set up a welding current for welding our tin.
- The filler material was cleaned (cleaned the powder from the powder coating)
Now we need to try to put the details so that they are as small as possible. If there is another way of welding tin, then I would recommend it to you. Type of gas welding or semi-automatic. Why is it important to put doing? Because during welding, the parts are heated and cooled, and thus the expansion and reduction occur at the heating site. You did not notice when you cook something that is thin and easy of a can style you think that the item seems to be stirring? This is called the welder leads. Some people say: Oh look at how the metal came! It was probably heard many times. So put the do and press on top or secure temporarily, leave only the place where you need to weld the parts. If the details are not large it is not necessary. I'll take an example with two sheets. Put two sheets on the work surface. It is flat and made on it are located in the butt. there is no possibility to strengthen it. After welding two metals shrink to each other, so what else do you say whence this angle was formed. It is formed as a result of deformation of the metal. That such it was not necessary to put these two parts not much under the opposite angle, so that after the joining of the details everything became exactly. In degrees, I do not know how many, but by the eye it is barely visible that the details are not exactly lying. Nearby it may even be imagined that they are exactly docked. All try on some kind of similar metal before welding, open your hands.
Sheet metal is a sufficiently popular material for the manufacture of many technical devices and structures. Sheet steel is designed for the production of load-bearing elements of bridges, beams, tanks, drains, housings of electromechanisms and other products. The only way to join such a sheet is to weld sheet metal. This is a completely reliable type of connection, the features of which depend on the thickness of the metal and its location in space.
Welding methods for sheet metal
Metallic sheets of medium thickness are cooked in a stepwise fashion. The entire welding strip is conventionally divided into sections of 10-20 cm, after which these sections are welded alternately. Each subsequent seam overlaps the previous seam by 1 cm. This technology avoids the temperature deformation of the metal.
Welding of thin sheets of metal is usually made by butt, with flanging of edges. Also, butt joints are allowed on the lining, without flanging. There is welding of cylindrical products. For example, welding to the flanged bottom of a cylindrical body or welding to a flanged bottom shell.
Welding of thick metal (more than 4 mm) is performed in several passes. This is the so-called multilayer welding. Welded seam is filled in several times. Before each subsequent layer is applied, the previous layer of descaling is cleaned. Multilayer welding is more reliable, but leads to an increase in consumables.
Preparation of sheet metal for welding works
All products in places of edges and adjacent areas should be thoroughly cleaned from paint, dirt, oil, rust, scale and moisture. Cleaning is done with a metal brush, a grinder or a burner flame. The best result is a symbiosis of these methods. The edges are machined using a grinding machine or a milling machine.
They must be beveled at a small angle to comply with technology welding works. High-quality welding of sheet metal butt-end is possible without proper processing of the edges.
Depending on the design of the future product, parts are assembled and fastened together by means of various devices. Clamps are used for fastening sheets, wedges, locks, levers, tightening corners. For thick pulling products are used jacks. In the shop conditions, the welding of sheet steel is ensured by special clamping mechanisms.
To ensure the immovability of the seam, the products are fastened with tack welds. Their size depends on the thickness of the sheet metal and the total length of the seam. For thin sheets, the length of the stitch is up to 0.5 cm, and for a thick metal it can reach up to 3 cm. With a metal thickness of 1 cm or more, mitts are usually not used.
In this case, wedge screeds are used, allowing minor displacement of parts during the welding process. Also, triangles and clamping straps can be used.
Technology of welding sheet metal
Welding of the rolling metal can be carried out butt-end or with overlap. Vertical seams it is recommended to perform butt joints, and it is better to do circular circular joints with an overlap. The first step is to weld the transverse seams, and then work on the longitudinal seams.
The gaps between the joined products should be about 1 mm. This is necessary to prevent deformation of products. It is recommended to weld sheet metal from the middle, gradually moving to the edges.
Welding is performed at an angle of 70-90 degrees. In this position, the maximum weld penetration is performed.
Welding any sheet metal in accordance with the recommendations, receive quality welded products of the proper strength.
The welding process by the inverter is designed to weld a thin metal, forming a qualitative weld, as for most parts the thickness of the sheet is about 5 mm wide, and many varieties of welding are not suitable for this process. This kind of welding has good quality, if we take into account the parameters with strength of viscosity and plasticity. There are parameters due to which welding of thin metals becomes more qualitative:
·Reliability;
· Resistant to corrosion reduction;
·Flexibility;
·Viscosity.
Varieties of thin-sheet metal welding and its features
To make welding of thin metals it is necessary rather often as the majority of details consist precisely of such sizes:
· Motor boats;
· Cars.
To make qualitative welding will turn out after taking into account all the nuances of the forthcoming work. The main problem is that thin blanks are more likely to be burned by an electrode, after which the workpiece will become unusable. It is required to have a lot of experience working with electrodes to weld this kind of metal, otherwise the best quality is achieved by the seam and the connection of the metal surfaces. Still there are difficulties in implementing the correct work with the arc, and choose the necessary parameters for joining the workpieces.
Necessary conditions to be observed when joining thin metals
Before the beginning of the process, it is required to select the required electrode thickness by the thickness, which will be identical in coincidence with the forthcoming workpiece for welding. The current is set according to the thickness of the electrode. Also an important choice is coating the electrode, since for this process a special one is needed that melts over a long period.
To ensure good work in the welding of parts, an inverter is used. Thanks to the latest developments of devices, it is possible to easily produce welding processes for thin metals, which have a low weight and a high level of productivity. The inverter is welded to a constant current source. To weld a thin metal, you can use electrodes of different brands. While working on this device, it is recommended to adjust the current by about 10-15 A. To create a better weld, use electrodes 1.6 mm wide.
The inverter can be adjusted to different voltages or amperes, for more convenient welding. Energy costs are not significantly large, unlike a transformer or rectifier, and the efficiency is 90%.
The device of the device for welding of thin metal
In the beginning, it is required to investigate the mechanism of the mechanism for welding, which is relatively difficult due to the application of high voltage, current and maximum frequencies. During the welding process, voltage transitions occur, from alternating current in 220V to direct current with a high frequency. Also, the battery pulses are included in the presence of the inverter, which consist of modules. Thanks to processors with programmable microcircuits, the work of the elements of the apparatus for welding is coordinated.
Programs that are produced by the inverter:
· Elimination of the voltage at the moment of closing the arc for welding;
· Additional current pulses are formed;
· Ensuring the destruction of the barriers of liquid metal with short arc welding.
The process of working with the welding machine
There are many things that you can do in your own home with welding. It is much easier to fix the car, to join the workpieces from the metal, when there is an inverter for welding at hand.
For work it is required to acquire the following devices:
· Electrodes;
· Apparatus for welding;
· Gauntlets;
·A hammer;
· Metal brush;
·Welding mask;
· Refractory or simply dense overalls;
· Presence of water, to eliminate various possible sources of flame.
For the required quality of the seam in the beginning, you should adjust the appropriate voltage in the apparatus and the electrical network. It is required to inspect the plug, socket, cable and check their serviceability. Unequivocally forbidden to work on the machine in poor working condition.
It is recommended to place the device on a firm surface, and also check the grounding. Having detected the thickness of the workpiece, the corresponding electrodes are selected, and the amount of current is regulated by the handle on the apparatus.
Before the welding process, it is required to clean up the future part by removing the dirt and rust with a metal brush or sandpaper. Then you need to grip the metal sheets. The electrode is clamped into the holder, and the welding arc is ignited by touching or tapping movements over the metal workpiece. It is necessary to carry out the correct current parameters, and then lead the arc in the desired position. At the end of the process, it is recommended to allow time for the cooling of the part, then to repel the slag and clean it to a noticeable gloss surface.
Weld arc control process
During the welding process, it is necessary to observe the desired distance of the burning arc, from the electrode to the metal. The same dimensions of the resulting gap are considered stable in the guarantee of a literate implemented technological process. If the given dimensions between the intervals are shortened, a weld seam curved by the welding arc will be obtained, with the participation of the molten lateral part of it. If you carry out work at the longest distance, then high-quality welding will not work, because the arc is distorted, and the metal is welded with distortions to one side. If it is true to observe the specified clearance when welding, you can eventually produce a smooth, neat seam.
Formation of a simple welding seam with an inverter
When the arc appears, it is in her power to cover all the base metal, and move the entire weld pool to its original position, creating a seam. The main task of the welder is to ensure that the seam is aligned with the metal.
In such cases it is recommended to keep the dimensions of the seam in the field of view on an ongoing basis. You should also place the bath in a circle. Welding of metals with the help of an inverter is required by smooth movements, forming a seam, while at the same time looking for its appearance from one edge of the metal sheet, and then controlling its appearance by the welding bath.
If the electrode is kept close to the metal plate in the process, a convex seam will form. Many experienced masters achieve the formation of a flat seam and the movement of the bath, by the necessary change in the angle of inclination of the electrode.
Features in welding with inverter metal with small thickness
The welder needs to pay attention to the polarity of the electrode, because their size affects the durability of the weld, and the strength of the entire weld.
Thanks to electrodes with reverse polarity, it is easy to achieve a deep seam formation. At the beginning of the process, you need to determine which charge to use and how to connect it. The positive charge is heated much more. When starting the process, it is necessary to adhere to the required angle by an electrode of 30 degrees, approximating it by the necessary distance, you need to form a red spot before the red-hot drop of metal appears. Weld appears after all the drops are connected on metal sheets to each other.
Advantages of inverter welding with rectifier
Metals with fine dimensions have low material consumption, so their need for welding is widely in demand in industrial areas. In principle, you do not need to have great skills to connect the metal, thanks to the constant welding arc and the quality of the final results. In most cases, where the main value is the quality of the seam welded, inverters use for arc-arc welding. If the welding process is carried out using a semi-automatic machine, the inverter can control the movement of the metal, and reduce its splashing.
The most advanced technology is plasma arc welding. When this kind of welding is used, the productivity of labor increases, due to changes in cutting speed, while the formed arc is constant.
Welding equipment should be treated carefully and carefully, to avoid various malfunctions. The technician can produce incorrect parameters, and as a result, the operation of the part can be disrupted. If the welding process can not be performed while the machine is switched on, the first thing to check is to inspect the cables. If the welding arc is not strong enough, it is necessary to check the current, because of which the inverter may not work, otherwise it should be sent to the service department for repair of these devices, a probable problem will be a violation in the operation of the module.
How to choose the right machine for welding
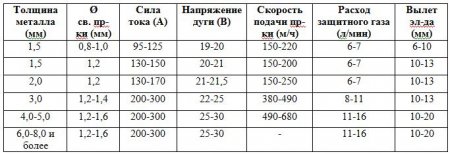
Before you proceed with the purchase of this unit, you should determine with which metals the work will be carried out in the main. It is necessary to take into account the parameters of the welded material, and the electrodes need to be selected according to the composition with the metal or with the thickness of the workpiece. The current parameters are adjusted to the required qualities and composition of the metal, and its dimensions.
There are three modes in which the welding machine can work:
·Extreme;
·Average;
· Prolonged.
When the mains voltage is reduced to about 190V, a low amperage will occur during the process. It is not recommended to use cables that are 15 meters or more in length, since the current distribution along them will also lead to a low welding current.
Do not forget that it is recommended to keep an account of the electrical supply network, since at a low value it is required to use devices that can operate in a voltage fluctuation of 220V plus or minus 5%. Apparatus that has idling, such can be done in wet rooms, various cellars or sewer systems.
Operation of the inverter is not performed if the temperature is below 0 degrees Celsius, and sudden changes can lead to condensation inside the circuits.