How the piping is piped with polypropylene. Typical errors in the connection. Systems with natural circulation
Pipes made from polypropylene using innovative technologies have a lot of priorities, among them cheapness and resistance to aggressive factors occupy leading positions. The affordable products serve owners no less than expensive counterparts. On the walls they do not settle the contraction diameter of the pipeline plaque. The connections are made by soldering, so that the piping of the boiler with polypropylene becomes "monolithic", that is, there are not exactly leakages typical for pipelines with poorly installed leakage fittings. However, there are some nuances about which it is necessary to know the owners of houses, choosing polypropylene for the device of communications.
Specificity of piping with polypropylene
A weighty advantage polypropylene pipelines recognize the possibility to create a contour of any complexity, which in principle is not very interesting for those who are using the piping for their own hands for the first time. The simpler the scheme of the future system, the easier it will be to implement the idea. And the heating output is inversely proportional to the degree of complexity: the simpler, the more efficient. To make connections home master can use, as welding technology, and selected strictly in the size of pipes fittings. However, at the slightest "shifts" in the places of installation of fittings, the system may start to flow slightly.
With the help of polypropylene pipes, it is possible to create heating circuits of any complexity, but it should be remembered that the complexity complicates the installation and reduces the efficiency of the heating system
It is desirable that the created heating system has the least number of connections. If you can make a smooth transition, you need to use it.
The polypropylene pipeline will operate without problems for 40 years, guaranteed by the manufacturer, it will withstand pressure, the values of which exceed 25 bar. Without damage to the structure of the material, a coolant with a temperature of 95º can circulate through the pipes. However, there is a restriction, which is necessary to take into account, if binding is carried out gas boiler.
The gas connection to the boiler must be rigid, the building requirements dictate the use of metal elements for the connection and the use of a paronite gasket
The gas connection to the boiler must have a rigid connection. Building requirements require a metal pipe and docking with a heat generator through a metal overhead or an "American". Use only a gasket of paronite. Rubber materials, tapes, towels are prohibited. Paronite, obtained by vulcanizing a mixture of asbestos fibers, mineral fillers and rubber, perfectly holds the shape, ensures tightness and does not burn. Other cushioning materials tend to ignite, and rubber sandwiched between the elements can reduce the size of the gas passage. If the diameter of the passage is reduced, the gas supply will be reduced and the boiler will not supply the required amount of heat.
Determination of the location of the boiler in the common system
The boiler is the main "organ" of the heating circuit, the choice of the binding scheme depends to a large extent on its type. The floor heat generator can not be located at the highest point of the pipeline layout. This is the main rule of its installation. In the event of non-compliance with this condition, in a boiler that does not have an air vent, they will accumulate air congestion. The pipe of the supply line leaving the boiler without an air vent should be strictly vertical.
The presence of an automatic air vent installed in an electric or gas boiler can be determined by the nozzles located in the lower part of the unit, a supply line and a return line
On the presence of an automatic air vent installed in the boiler, "tell" the pipes located at the bottom of the unit, intended for connection to the heating network. They usually have a wall-mounted electric or gas equipment. This feature of the scheme of the walling of the wall heating boiler must be taken into account, since most monoblock boilers mounted on the wall can independently be freed from the accumulated air.
If the boiler was purchased without expansion tank, the pump, the pressure adjustment device, all the missing components can be purchased separately, the safety group can be installed, both at the inlet and outlet of the coolant
Boilers can now be purchased, as with the expansion tank, and the security team, and without the entire list of additional devices. If the purchased unit does not have the listed devices, they can be purchased separately and included in the circuit. People who build, they mostly do not need, and those who arrange the outline with forced heating, be sure to be necessary.
Ways to bundle heating boilers
By the principle of circulation of the coolant through the heating circuit, all types of strapping are divided into systems with natural and forced movement. In the latter of these groups there are subgroups, the division into which is made by the type of wiring.
Option # 1 - circuits with natural circulation
This group includes the simplest and most accessible self-assembly system. Characteristic of this heating, also called gravitational - the absence of a pump that stimulates the movement of the coolant. That is, the movement of heated water to heating appliances and cold outflow is accomplished on the basis of physical laws without human intervention and mechanisms. The simplest scheme for tying the heating boiler is suitable for small country houses. It will not cope with the maintenance of multi-storey buildings and large-area buildings.
Tying the heating boiler with natural circulation - the best option for self-installation, the structure includes only a boiler, radiators and expansion tank
Advantages of gravitational heating:
- the easiest installation;
- work that does not depend on the availability of electricity and is related to the supply of this energy carrier interruptions;
- budgetary size, both construction and maintenance;
- almost uninterrupted functionality, because in their composition there are no devices capable of failing at the wrong time;
- the ability to repair the system on its own, if, of course, it will not be necessary to repair the boiler.
There are some disadvantages too. Required accurate calculations the diameter of the pipes in order for the circuit to fully perform its functions. The diameter will be considerable, which does not always suit the owners of compact cottages. The interior looks natural circulation system is not too presentable. It is impossible to regulate its functionality. However, the scheme of tying the floor gas boiler or wall-mounted unit can be upgraded by insertion circulating pump, which can be used if necessary.
Option # 2 - forced type heating
The circuit with forced movement of the coolant is more comfortable, its owner can control its operation. It will be possible to choose the optimal temperature for each room, and the mode specified by the host will be automatically maintained. It is only necessary to take into account that such a strapping of a floor boiler and a wall heat generator requires power supply. In case of interruptions, which are not uncommon for domestic networks, the circuit will not work. If electricity is not supplied, this type of heating will have to be abandoned.
The classical version of the piping of a heating boiler requires balancing and compulsory maintenance of appliances
- a complex scheme of strapping, including a mass of flowmeters, devices for venting air, distribution manifolds, valves, etc .;
- mandatory balancing of devices;
- the need for regular, expensive service;
- professional installation and repair, which takes a lot of money;
- high cost of appliances and services installers.
The number of devices built into the network can be reduced by applying the principle of primary secondary rings. The protection and control devices will be smaller, but each of the arranged heating rings will need to be equipped with its circulation pump. The systems consisting of several rings with a floor boiler with a power of less than 50 kW are equipped with comb collectors, which guarantee a uniform supply of coolant to the devices.
What is the strapping?
What is included in the binding system?
Tying Options
Strapping Elements
Other Strapping Elements
The cauldron can be called a heart heating system. However, in order for the heating system to work effectively, it is not enough just to select the boiler correctly and connect it correctly. It will be necessary to select correct scheme heating. If at least one device is incorrectly connected, this will severely affect the entire system. Therefore it is important to consider what the piping of the boiler means and what is the sequence of its installation.
What is the strapping?
In fact, this is all equipment intended for efficient operation of the boiler and the successful delivery of coolant to the radiators. The harness provides several advantages:- provides the optimum temperature in the heating main,
- controls the amount of coolant in the system,
- removes air from the main line,
- guarantees the safety of the boiler against overpressure,
- does not allow devices to clog with slag, squeaks and other debris,
- controls the heating time heating devices,
- allows you to connect different contours heating and adjust them to the required temperature,
- effectively distributes heat through radiators.
What is included in the binding system?
This includes different instruments. Here is a list of the main elements:- expansion tank,
- pump,
- distributive valve,
- balancing crane,
- manometer,
- drain and ball valves,
- valves (air, through, return, safety),
- filter.
Sequence of installation works
Regardless of the wiring options, it is assembled in one sequence.- First, you are advised to carefully read the instructions for all equipment and its characteristics. It is important that during the installation of the heating system did not have to run to the store and change the device.
- Boiler installation.
- Installing the expansion tank.
- Selection of the place for the collector. Here you need to be careful not to confuse the supply line with the return. This information is on the case of the device.
- Safety devices are installed on the supply line.
- Then the pump is mounted.
- To the trunk, devices are installed to improve the operation of the system: a filter, an air vent, cranes, valves, control devices and so on.
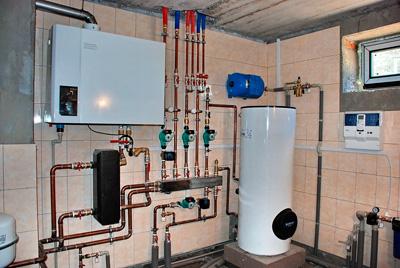
Adhering to this order, you can make a successful binding of the boiler.
Tying Options
There are 4 main and most common ways:- with the circulation of natural,
- with forced,
- collection classical,
- on primary-secondary rings.
1. Stroke with natural circulation. This option is the easiest. Here, as the name implies, there is no pump, and the coolant moves along the main due to physical laws. All settings are set manually, and also it is necessary to observe the operation of the system. In order for this heating to work properly, you need to consider some tips:
- the pipe should be of a large internal diameter (from 32 mm),
- the boiler is installed below the radiators,
- the slope of the pipes should be at least 5 mm along the course of the coolant,
- the minimum number of rotations of the pipes, so as not to interfere with the natural course of the liquid in the pipeline.
2. Forced circulation. This type of strapping is the most common. It has many advantages. One of the most important is the temperature adjustment of each battery. Principle forced circulation consists in the fact that the heat carrier can flow along the main line at high speed, thanks to the pump. The only drawback of this option is the dependence of the pump on electricity. When it is turned off, the pump stops working. However, there are 2 ways to solve this problem:
- installation of a bypass pipeline (bypass), which will enable the system to switch to natural circulation;
- arrange a high-quality emergency scheme, through which it will be possible to lose excess heat;
- install a system autonomous power supply (uninterruptible power supply).
3. Collector wiring
. Although this version of heating is the most expensive and complicated in terms of installation, but it is the most efficient, convenient and energy-saving. Its essence is that all pipes from the boiler pass through special device, which is called the collector. In this node there are various valves, cranes, air taps, measuring devices and so on. From the collector there is a separate wiring to other devices. There are a number of advantages that appear due to this method:
- Each heating element is controlled separately from the collector box, which makes it possible to disconnect any without disturbing the operation of the entire highway.
- Throughout the highway the temperature is the same.
4. Strapping on primary secondary rings. This method is often used in buildings where there are many consumers. More than one circulating pump is used here. The essence of the work of this wiring is the following: to the small circuit where the heated coolant is located, pumps are connected, which, if necessary, take this water to the consumer. There are 2 types of circuits connected to the boiler:
- Mixing. Here, the temperature of the coolant is affected by how open the damper is.
- Straight lines. In this case, the liquid is heated from the burner.
There are also 2 ways to connect the circuits:
- Two-way connection, when the coolant is supplied by pumps.
- In the three-way connection, each circuit has a separate tap, and is connected to a boiler in which the coolant is heated.
- Cold water is supplied from the water supply.
- The pump switches to an additional power source (for example, a battery). Using this option, it is important not to forget to monitor the charging of this source.
- Installation of an additional circuit with natural circulation. This small circuit removes heat after the pump is turned off.
- Simultaneous use of two circuits. When the power-dependent branch stops working, the loop with natural circulation continues to heat the room.
Strapping Elements
Now it is worth paying attention to the main elements that are used when tying the boiler. You should consider the features of mounting each of them.Boiler
It is very important to connect the boiler correctly. On this depends not only the effective operation of the entire heating system, but also the safety of people in the room.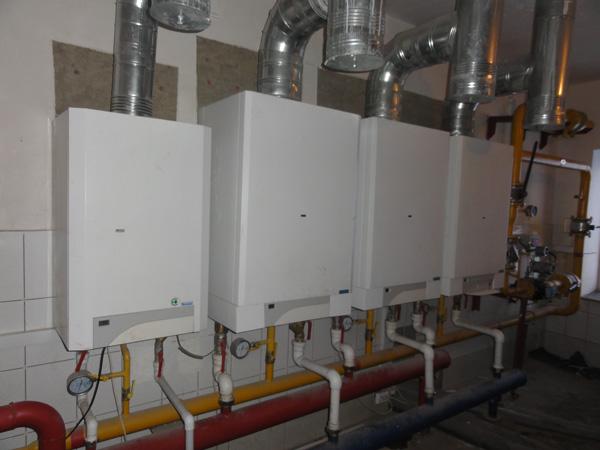
To begin with, a little about installing gas boilers. Since the connection occurs to a pipe in which gas is under high pressure, it is forbidden to connect this equipment independently. Therefore, acquiring a gas boiler, the next step will be the call of specialists.
The electric boiler is not difficult to install. Basically, the complexity is related to the adjustment of automation.
Now about the installation of a boiler working on liquid fuel. It's better that experts do it. However, there are basic principles that must be taken into account for the successful operation of this unit:
- Correctly install containers for waste oil or diesel.
- Ensure the necessary conditions, for safety requirements. Neither the fuel nor the boiler should be close to flammable materials.
- The burner is connected using a duct with a filter.
- A pump can be connected to the system, which will give a uniform fuel supply.
- First you need to build a foundation. It can be made of clay or concrete. Above him lay a sheet of iron or asbestos.
- Place the boiler below the radiators. This is especially important if natural circulation.
- Then connect it to the chimney through chimney. The connection must be sealed to prevent the release of carbon monoxide.
- For better ventilation of the room, it is advisable to install a fume hood.
Pipes
Pipes are an important component of the boiler's piping. But it is not easy to decide which pipes to use, due to the fact that the popular versions are metal plastic and polypropylene. Therefore, it is worth paying attention to everyone.Metal-plastic consists of 5 layers, which includes 2 layers of plastic, 2 glues and 1 aluminum. The diameter of such pipes is from 16 to 63 mm. They have such advantages:
- increased plasticity, which simplifies installation,
- low thermal conductivity,
- not subject to corrosion,
- easily repaired,
- do not need an expensive tool for installation,
- good noise absorption.
- at a mechanical pressure there is a dent,
- it is necessary to carefully check the connections for leakage during installation.
- if the water freezes in them, they do not collapse,
- resistant to both acids and alkalis,
- are not afraid of mechanical damage,
- are connected by a method of soldering, which eliminates leakage over time.
If you pay attention to the shortcomings, you will see the following:
- difficult to repair if damaged,
- for installation, expensive equipment is required,
- at a high temperature, pipes are elongated.
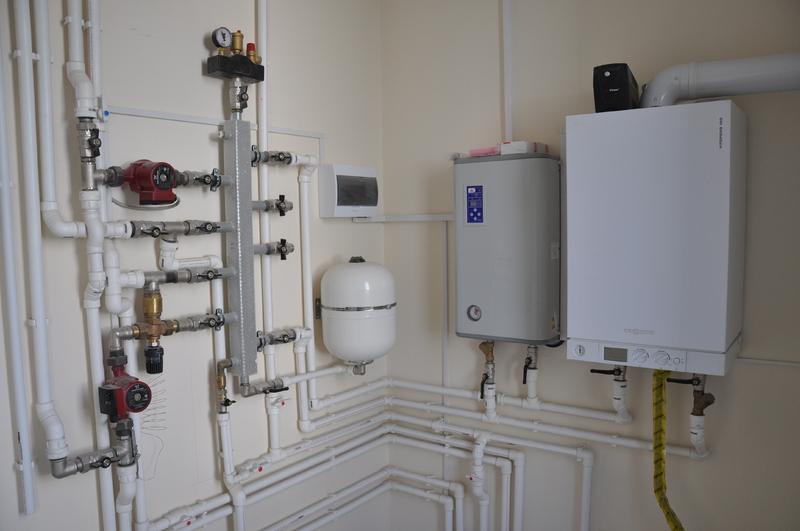
So, choosing pipes for tying, you need to consider your needs. If important indicators such as diameter, frost resistance, endurance to damage, reliability of connections, polypropylene pipes are suitable. However, if it is preferable to endurance to high temperature, ease of repair and installation, then the metal plastic wins.
Other Strapping Elements
The expansion tank plays an important role in the system. It does not allow the water to expand from the heating, create pressure on the components of the heating main. An open tank is installed at the highest point of the system, into the outflow pipe. Installing the tank closed type with a membrane, should adhere to several principles:- choose a free place for access, near the highway,
- mounting is made on brackets and at plus temperature,
- first connect the meter, and then the pressure reducer,
- a safety valve is mounted on the flow pipe.
- it is placed near the cauldron,
- on the highway it is necessary to organize a bypass that will allow to disconnect the pump, not breaking system work,
- installation of shut-off valves, filter and check valve.
- this group is mounted on a pipe that exits the boiler,
- the boiler must be below the safety valve,
- put first a pressure gauge, then a safety valve, and then an air vent.
Bottom piping
Private houses, especially suburban houses, are traditional units. Heated by means of firewood or coal, peat or pellets, they have long sought the glory of reliable heaters. Of course, there is no need to talk about the absolute quality of exploitation, because they have certain drawbacks. But the availability and cheapness of fuel played a role. In this article, we will discuss how to properly tie a solid fuel boiler, and what kind of pipe layout is best to choose. So, the scheme of tying the solid fuel boiler.
Strapping schemes
Let's start with two simple positions:
- The first concerns the construction of the solid fuel boiler itself. Remember - in none of its models and modifications you will never find built-in circulation pumps and expansion tanks. They are selected separately. The first is for the capacity of the heating unit and for the area of the heated premises. The second - only from the calculation of the volume of the coolant. By the way, the volume of the expansion tank is always 10% of the total volume of the used coolant.
- The second position is, in fact, a question from consumers who believe that it is useless to fence the garden in this regard. Connecting a solid fuel boiler is simple - through two pipes, one of which connects to the supply circuit of the heating network, and the other - with its reverse circuit.
The second position correctly sets the connection tasks for the installers. But this is the simplest scheme. By the way, the one who decided to install the solid fuel boiler himself, chooses this option of connection and strapping. And what for to be excruciated, if there is a simple and thus effectively working scheme.
But let's face it. The above scheme of strapping is not the only one. There are more complex options based on one very important rule. By the way, practically all producers of solid fuel boilers this rule indicate as a warning in the operating instructions of the heating units.
It says that the temperature hot water In the reverse circuit at the entrance to the solid fuel boiler should not be below + 60 ° C.
Why such tight restrictions?
- Firstly, this is the only way to avoid a large temperature drop inside the heat exchanger, which has a positive effect on its service life.
- Secondly, this is the only way to avoid condensation of wet fumes inside the boiler furnace. The appearance of even a few drops of water on the walls of the combustion chamber gives an impetus to the formation of tar fuel on the walls. Soot and moisture cause such a negative effect.
Now we are interested in the question - how to make sure that all these processes do not arise, and the temperature in the reverse does not fall below + 60? There are several options.
First option
This is the simplest, with regard to the complex tying of solid fuel boilers. To do this, it is necessary to insert a so-called mixing unit into the heating system. Many may think that this not only complicates the scheme, but also increases its cost. In fact, the mixing unit is an ordinary pipe jumper that connects two - feed and return. It is usually cut one end into the area between the circulation pump and expansion tank, and the second - to any point of the feeding circuit.
Why is this jumper necessary? It plays the role of a mixer, which includes hot water from the feed loop and passes into the return flow. Thus, if necessary, you can increase the temperature of the coolant in the reverse section of the heating network. A jumper valve is necessarily installed on the jumper.
That is, the heating operates in the normal mode until the temperature in the return drops. As soon as it reaches a critical level, the automation system is triggered and a jumper opens. If you installed a simple solid fuel boiler in your house without a complicated automation system, then you will have to control the temperature of the coolant yourself and manually mix the media by opening and closing the shut-off valve. Therefore, the installation of a thermometer at the entrance to a solid fuel boiler is a prerequisite.
The second option
Solid fuel boiler in the heating system
How does a simple solid fuel boiler work without an automatic fuel supply? You manually load wood, peat, coal and so on into the firebox. That is, you are completely tied to the heating unit. A little late with the bookmark, and we can assume that immediately lowered temperature regime inside the premises of the house.
What options do specialists offer to ease your life and reduce dependence? This problem can be solved by installing a buffer tank. What is it, and where is the binding of solid fuel boilers?
To begin with, the buffer capacity serves as a thermal energy storage. There is water in it, which is heated by the supply circuit of the heating network. As soon as the fuel burns in the furnace of the boiler, and you do not notice it, the coolant will begin to lose its temperature. So the installed buffer capacity, or rather, the hot water in it, begins to give its heat to the heat carrier. This prolongs the operating time of the heating system.
What will be different from the previous options? The container installed in the circuit divides the entire heating system into two sections:
- In the first there is a heating boiler.
- In the second one there are radiators of the heating system.
And now, most importantly, as for the binding of the boiler with buffer capacity. Everyone knows that TT boilers are difficult to control and regulate. It is almost impossible to manage them. Especially, when you forget to make an accurate bookmark of fuel. For this purpose it is recommended to install one more mixing unit. That is, one is already installed in the first section and is designed to increase the temperature in the reverse circuit of the heating system. The second node should be located in the second section after the buffer capacity. Its purpose is to reduce the temperature of the coolant at the peak of the operation of the solid fuel boiler.
What do we get as a result? We have one strapping scheme, where a buffer capacity is installed. So there might be a jumper in it, or maybe not. It all depends on how often you make a bookmark of fuel. If you own a boiler with automatic fuel supply to the combustion chamber, then you can do without a jumper. In general, in this case, you can use the simplest scheme of tying.
Emergency scheme
Connection wiring diagram
We return to the proposition that the management of solid fuel boilers is the number one problem. In them, overheating of the coolant is a common thing, therefore, without exception, all manufacturers try to find ways to cool hot water before it starts to turn into steam. What do they use? Which methods are effective, and which are not very?
Let's consider three basic methods of cooling the coolant:
- Two heat exchangers are installed in the combustion chamber of the boiler, which are in close contact with each other. One works for heating the coolant, and the second is used as a refrigerator. Its inlet branch is connected to the water supply system, and the opposite one to the sewage system. If you need to lower the temperature of the coolant, you just need to open the valve on the water pipe and run cold tap water into the second heat exchanger. This is the principle of work.
- The scheme is almost the same. But only the second heat exchanger is installed inside the first one. With this arrangement, the coolant temperature drop is several times faster and more efficient.
- And the last option. There is no second heat exchanger in it. In its branches - incoming and outgoing - are connected two pipes, which on one side are connected to the water main, and on the other - to the sewerage. At the junction of the pipes, a valve is installed that opens or closes access cold water in the heating system of the house. Of course, this coolant becomes more heated in the heating system, and therefore the outlet pipe is connected to the sewage system.
Let's put it bluntly - the temperature reduction scheme is rather strange. But surprisingly, boilers with such a design are present on the market, and even service centers are organized for them.
Additional schemes
Connection of two boilers into one system
And one more addition, which directly relates to the topic of the article. Everyone knows that the supply of electricity in country houses occurs with periodic trips. Therefore, the circulation pump will fall out of the system, preventing free passage of the coolant. What to do? The output is known for a long time - to install a bypass that cuts the pump from the circuit. It seems to be a simple knot, but it is necessarily included in the binding scheme, so you can not forget about it.
And the last. At present, so-called combined boilers are in fashion. A good invention, which helps to use two types of fuel, replacing each other. But what to do for those who have already installed a solid fuel boiler, and want to have a spare option? The only solution is to install one more heating unit, working, for example, on gas or electricity. Or rather, you need to make it basic, and TT boiler auxiliary.
In this case, a parallel installation is added to the piping in parallel with a cut-in into the feed and return circuits. It is obligatory at the junction of two joints to install shut-off valves or latches. If the system is automated, it is better to take a three-way valve.
Conclusion on the topic
As you could see, the scheme of tying a solid fuel boiler is a very difficult task, as it may seem at first glance. See how many nuances. It seems that only a few devices are crashed, but their use is carefully thought out and necessary. And the one who chooses one of the above schemes, must be aware that all of them are not as simple as they seem. Correct connection this or that node, the sequence of docking and so on - all this in the future will necessarily affect the efficiency of the heating system at home.
The creation of a heating system involves the connection of the boiler and radiators (radiators, convectors and a warm water floor). Also, there must be security devices in the system. The procedure for connecting all this farm is called "tying the boiler."
What is the strapping and what is it made of?
In the heating system, two main parts - a boiler and radiators or warm floor. The fact that they are connected and provides security - this is the harness. Depending on the type of installed boiler, different elements are used, therefore, they usually consider the binding of solid fuel assemblies without automatics and automated (more often - gas) boilers. They have different operating algorithms, the main ones are the possibility of heating the boiler's TTs in the active combustion phase to high temperatures and the presence / absence of automation. This imposes a number of limitations and additional requirements, which have to be performed when tying the boiler, which operates on solid fuel.
An example of piping the boiler - first comes copper, then - polymer pipes
What should be in the harness
To provide safe work heating the piping of the boiler must contain a number of devices. Must be:
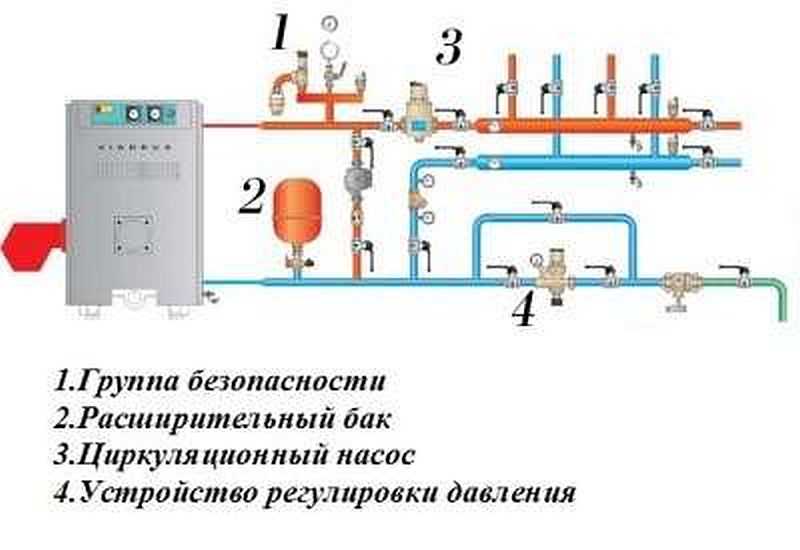
Some of these devices are already installed under the casing of a gas wall-mounted boiler. The strapping of such an assembly is very simple. In order not to complicate the system with a large number of taps, a manometer, air vent and emergency valve are assembled into one group. There is a special case with three outlets. The appropriate devices are screwed onto it.
So the security group looks like
Establish a safety group on the supply line immediately at the outlet of the boiler. Set so that it is easy to control the pressure and you could manually relieve pressure if necessary.
What pipes to make
Today, metal pipes are rarely used in the heating system. They are increasingly replaced with polypropylene or plastic. The piping of a gas boiler or any other automated (pellet, on liquid fuel, electric) is possible with these types of pipes.
When connecting a solid fuel boiler, at least one meter of pipe on the pitch is impenetrable to make a metal pipe and, best of all, a copper pipe. Next, you can put the transition to metal plastic or polypropylene. But this is not a guarantee that polypropylene will not collapse. It is best to make additional protection against overheating (boiling) of the boiler's TT.
Which polymer pipe is better? Polypropylene or metal-plastic? There is no unequivocal answer. Piping with polypropylene is good in the reliability of joints - properly welded pipes are a monolith. (). But the maximum permissible temperature of the coolant in the system is not higher than 80-90 ° C (depending on the type of pipe). And then, the prolonged exposure to high temperatures leads to the rapid destruction of polypropylene - it becomes brittle. Therefore, the piping of the boiler with polypropylene is made only in low-temperature systems on the basis of automated boilers.
If there is protection against overheating, the piping can be made with polypropylene pipes
Metalloplastik has a higher operating temperature - up to 95 ° C, which is enough for most systems. You can also make them the binding of a solid fuel boiler, but only if one of the systems protects against coolant overheating (described below). But metal-plastic pipes have two significant drawbacks: narrowing at the junction (fittings construction) and the need for regular testing of the connections, as they flow over time. So the piping of the boiler is made of metal plastic, provided that water is used as a coolant. Non-freezing liquids are more fluid, because in such systems, it is better not to use compression fittings - they will still flow. Even if you replace the gaskets with chemically resistant ones.
Tying of gas boilers
Modern gas boilers have good automation, which controls all parameters of the equipment operation: gas pressure, presence of a flame on the burner, pressure level and temperature of the heating medium in the heating system. There is even automation, which can adjust the work to weather data. In addition, wall-mounted gas boilers in most cases contain also such necessary devices as:
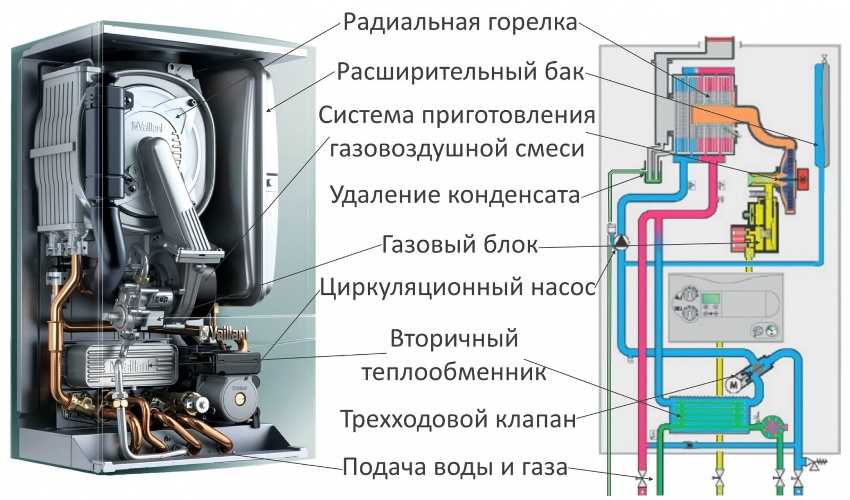
The parameters of all these devices are indicated in the technical data gas cats. When choosing a model, one should pay attention to them and choose a model not only in terms of capacity, but also in terms of the volume of the expansion vessel and the maximum volume of the coolant.
Scheme of the walling of a wall gas boiler
In the simplest case, the piping of the boiler contains only shut-off valves at the entrance to the boiler - so that, if necessary, repair work. Even on the return pipeline, coming from the heating system, put a mud filter - to remove possible contaminants. That's the whole strapping.
Example of piping of a wall gas boiler (two-circuit)
In the photo above there are angular ball valves, but this, as you know, is not necessary - it is possible to put conventional models, and the pipes to be deployed closer to the wall with the help of corners. Also note that on both sides of the sump there are taps - this is for the possibility of removing it and cleaning it without draining the system.
In the case of connection of a single-wall wall gas boiler it is still simpler - only the gas is supplied (connected by gas workers), the supply of hot water to radiators or water warm floor and a return from them.
Circuit diagrams for floor gas boilers
Floor models of gas heating boilers are also equipped with automation, but have neither a safety group, nor an expansion tank, nor a circulation pump. All these devices have to be installed additionally. The strapping scheme because of this looks a little more complicated.
On two schemes of classical piping of the boiler an additional jumper is installed. This is the so-called "anticondensation" loop. It is needed in large systems, if the water temperature in the return line is too low, it can cause condensation. To eliminate this phenomenon and arrange this jumper. With its help, the hot water from the feed is mixed with the return line, raising the temperature above the dew point (usually 40 ° C). There are two main ways to implement:
- with the installation of a circulating pump in the jumper with an external temperature sensor (and the photo above at the right);
- using a three-way valve (pictured below at the left).
In the circuit with the circulator on the jumper (condensation pump) it is made by the pipe at a step of smaller diameter than the mains. The sensor is attached to the return pipe. If the temperature drops below the set temperature, the pump supply circuit is switched on, hot water is added. When the temperature becomes higher than the threshold, the pump switches off. The second pump - the actual heating system, it works all the time while the boiler is running.
In the second scheme with three-way valve it opens a hot water pusher when the temperature drops (it is set on the valve). The pump is in this case on the return pipeline.
Tying the solid fuel boiler
Any owner of the boiler's TT knows that during the active combustion phase a lot of heat is released. Since time comes experience - when and how to cover the damper, for what period of time, etc. But it's worth a little distraction, and the water in the system overheats and can even boil. To prevent such a phenomenon, the piping of a boiler without automatics should contain several devices preventing the boiling of the system. Only in this case it is possible to arrange a house polymer pipes. Otherwise, sooner or later, the superheated coolant will soften the material, the pipes will break with all the ensuing consequences. Therefore, the binding of a solid fuel boiler, in addition to the traditional elements - the safety group, the expansion tank and the circulation pump - contains a substantial number of additional devices and usually requires quite substantial means.
The cyclical nature of the operation of solid fuel boilers leads not only to the boiling of the system, but also to the fact that the house is very hot (when the fuel is actively burning), it is cold - when everything is burned out. To eliminate these phenomena, there is a solution: install a boiler indirect heating or heat accumulator. Both are containers with water, they simply perform different functions and, accordingly, connect differently.
Tying with an indirect heater
With this construction, there is no sharp increase in temperature for the time of active burning that is usual for a solid fuel boiler. All because the volume of the tank is added, because there is almost no overheating of the water. Then, when the fuel burned out and in the usual system the house begins to cool down, the heat stored in the heating system continues to be consumed in the system with the TA. In this way, the temperature background is equalized and the time between the furnaces increases.
Such a binding of the boiler on solid fuel is more reliable and the wiring from the TA can be done polypropylene pipes, but the circuit from the boiler to the capacity must be done metal pipes. In this case, you can use steel, but better still copper.
Staging the boiler's CTs with a valve against overheating
The third way to make protection against overheating of a solid fuel boiler is to install an automatic overheating protection device. it special valve with a temperature sensor. The principle of operation is simple: if a certain temperature (usually 95-97 ° C) is exceeded, the valve opens the cold water inlet from the water pipe, and overheats the excess into the sewerage system. So, for example, REGULUS DBV 1-02, Regulus BVTS 14480 works.
Protecting the solid fuel boiler from overheating with the REGULUS DBV valve
Valves, though produced by the same firm, have a different structure and installation scheme. So REGULUS DBV is installed at the output from the boiler, has a built-in temperature sensor (the installation scheme is above). The Regulus BVTS 14480 boiler overheating protection valve has a remote sensor, can be mounted both at the inlet and outlet (installation diagram at the bottom). What is good about this option? The fact that it can work in systems with natural circulation - it does not need pressure for work.
Tying the heating boiler with the coolant boil-off valve
Their approximate cost - 40-60 € - is much less than the cost of installing a heat accumulator or an indirect heating boiler, but the problem of temperature fluctuation does not solve this problem. By the way, these valves can be used to improve the reliability of the circuit with an installed indirection and thus to precisely eliminate the possibility of boiling the system.
What else is needed in the system
The piping of the boiler will be incomplete if it does not have a tap for draining and filling the system. And it is better if they are separate. The exact location of the installation depends on the structure of the system, but there are certain rules:
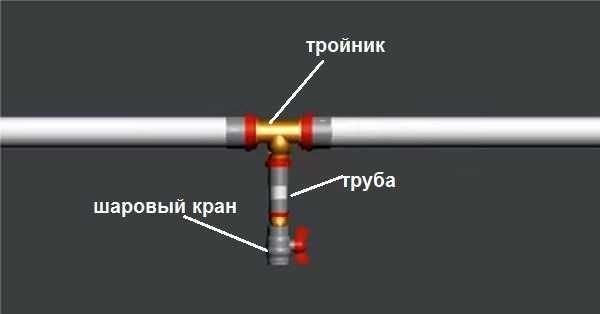
In some systems, drain and fill systems are made from one tap. This is possible if there is a pump that is pumped in and there is a pressure gauge to control the pressure created. If there is a separate tap for filling the system at a high point, you can fill it with gravity.