Диффузионная сварка. Типовой технологический процесс диффузионной сварки в вакууме
Отличительная особенность диффузионной сварки от других способов сварки давлением - относительно высокие температуры нагрева (0,5-0,7 Т пл) и сравнительно низкие удельные сжимающие давления (0,5-0 МПа) при изотермической выдержке от нескольких минут до нескольких часов.
Формирование диффузионного соединения определяется такими физико-химическими процессами, протекающими при сварке, как взаимодействие нагретого металла с газами окружающей среды, очистка свариваемых поверхностей от оксидов, развитие высокотемпературной ползучести и рекристаллизации. В большинстве случаев это диффузионные, термически активируемые процессы.
Для уменьшения скорости окисления свариваемых заготовок и создания условий очистки контактных поверхностей от оксидов при сварке могут быть применены газы-восстановители, расплавы солей, флюсы, обмазки, но в большинстве случаев используют вакуум или инертные газы.
Очистка поверхностей металлов от оксидов может происходить в результате развития процессов сублимации и диссоциации оксидов, растворения оксидов за счет диффузии кислорода в металл (ионов металла в оксид), восстановления оксидов элементами-раскислителями, содержащимися в сплаве и диффундирующими при нагреве к границе раздела металл - оксид. Расчет и эксперимент показывают, что, например, на стали оксиды удаляются наиболее интенсивно путем их восстановления углеродом, а на титане - за счет растворения кислорода в металле.
Сближение свариваемых поверхностей происходит в первую очередь в результате пластической деформации микровыступов и приповерхностных слоев, обусловленной приложением внешних сжимающих напряжений и нагревом металла. В процессе деформации свариваемых поверхностей, свободных от оксидов, происходит их активация, и при развитии физического контакта между такими поверхностями реализуется их схватывание.
При диффузионной сварке одноименных металлов сварное соединение достигает равнопрочное основному материалу в том случае, когда структура зоны соединения не отличается от структуры основного материала. Для этого в зоне контакта должны образовываться общие для соединяемых материалов зерна. Это возможно за счет миграции границ зерен, осуществляемой либо путем первичной рекристаллизации, либо путем собирательной рекристаллизации.
С помощью диффузионной сварки в вакууме получают высококачественные соединения керамики с коваром, медью, титаном, жаропрочных и тугоплавких металлов и сплавов, электровакуумных стёкол, оптической керамики, сапфира, графита с металлами, композиционных и порошковых материалов.
Соединяемые заготовки могут быть весьма различны по своей форме и иметь компактные (рис. 3.66, а) или развитые (рис. 3.66, б, в) поверхности контактирования. Геометрические размеры свариваемых деталей находятся в пределах от нескольких микрометров (при изготовлении полупроводниковых приборов) до нескольких метров (при изготовлении слоистых конструкций).
Рис. 3.66. Некоторые типы конструкций, получаемых диффузионной сваркой
Схематически процесс диффузионной сварки можно представить следующим образом. Свариваемые заготовки собирают в приспособлении, позволяющем передавать давление в зону стыка, вакуумиру-ют и нагревают до температуры сварки. После этого прикладывают сжимающее давление на заданный период времени. В некоторых случаях после снятия давления изделие дополнительно выдерживают при температуре сварки для более полного протекания рекрис-таллизационных процессов, способствующих формированию доброкачественного соединения. По окончании сварочного цикла сборку охлаждают в вакууме, инертной среде или на воздухе в зависимости от типа оборудования.
В зависимости от напряжений, вызывающих деформацию металла в зоне контакта и определяющих процесс формирования диффузионного соединения, целесообразно условно различать сварку с высокоинтенсивным (Р ≥ 20 МПа) и низкоинтенсивным (Р ≤ 2 МПа) силовым воздействием. При сварке с высокоинтенсивным воздействием сварочное давление создают, как правило, прессом, снабжённым вакуумной камерой и нагревательным устройством (рис. 3.67). Но на таких установках можно сваривать детали ограниченных размеров (как правило, диаметром до 80 мм (см. рис. 3.66, а). При изготовлении крупногабаритных двухслойных конструкций (см рис. 3.66, б) применяют открытые прессы. При этом свариваемые детали перед помещением в пресс собирают в герметичные контейнеры, которые вакуумируют и нагревают до сварочной температуры (рис. 3.68).
Рис. 3.67. Принципиальная схема установки для диффузионной сварки (a) и общий вид многопозиционной установки СДВУ-4М (б): и 1 - вакуумная камера; 2 - система охлаждения камеры; 3 - вакуумная система; 4 - высокочастотный генератор; 5 - гидросистема пресса
Для исключения возможности потери устойчивости свариваемых элементов, передачи давления в зону сварки и создания условий локально направленной деформации свариваемого металла в зоне стыка диффузионную сварку осуществляют в приспособлениях с применением для заполнения «пустот» (межреберных пространств) технологических вкладышей и блоков (см. рис. 3.68), которые после сварки демонтируют или удаляют химическим травлением.
Рис. 3.68. Технологическая схема диффузионной сварки с высокоинтенсивным силовым воздействием:
а - требуемая конструкция; б - заготовки для сварки; в - технологические элементы-вкладыши; г - сборка; д - сварка в прессе; е - демонтаж; ж -готовая конструкция; 1 - технологические вкладыши; 2-технологический контейнер; 3 - пресс
При сварке с высокоинтенсивным силовым воздействием локальная деформация металла в зоне соединения, как правило, достигает нескольких десятков процентов, что обеспечивает стабильное получение доброкачественного соединения.
Для изготовления слоистых конструкций (см. рис. 3.66, в) перспективна диффузионная сварка с низкоинтенсивным силовым воздействием, при которой допустимые сжимающие усилия ограничены устойчивостью тонкостенных элементов. При этом способе диффузионной сварки не требуется сложного специального оборудования.
При изготовлении плоских (или с большим радиусом кривизны) конструкций сжимающее усилие наиболее просто может быть обеспечено за счет атмосферного давления воздуха Q на внешнюю поверхность технологической оснастки при понижении давления газа в зоне соединения (рис. 3.69).
Рис. 3.69. Технологическая схема диффузионной сварки с низкоинтенсивным силовым воздействием плоских конструкций:
а - требуемая конструкция; б - заготовки для сварки; в - сборка; г - сварка; д - готовая конструкция; 1 - несущая обшивка; 2 - готовый заполнитель; 3 - технологические листы; 4 - мембрана
Наличие технологических элементов (прокладок, мембрани др.), обладающих локальной жесткостью и помещенных с внешней стороны свариваемых элементов, исключает возможность потери устойчивости обшивок в виде прогибов неподкрепленных участков. Величина сварочного давления Р ограничивается предельным напряжением потери устойчивости заполнителя σ п.з. (Р ≤ σ п.з.).
При изготовлении конструкций сложного криволинейного профиля может быть использована технологическая схема (рис. 3.70), при которой давление нейтрального газа воспринимается непосредственно внешними элементами самой конструкции, например, несущими обшивками, оболочками. В процессе сварки обшивки на неподкрепленных участках под давлением газа деформируются (прогибаются). Это ухудшает условия для формирования соединения, уменьшает сечение сообщающихся каналов, ухудшает аэродинамическое состояние поверхности. В этом случае Р ограничивается напряжением, при котором имеет место чрезмерная остаточная деформация обшивок на неподкрепленных участках (Р ≤ σ п.о.).
Рис. 3.70. Технологическая схема диффузионной сварки с низкоинтенсивным силовым воздействием конструкций сложной формы:
а - требуемая конструкция; б - заготовки для сварки; в - сварка; г - характер деформации элементов конструкции при сварке; 1 - внешняя оболочка; 2 - внутренняя оболочка
В ряде случаев можно исключить применение внешнего давления для сжатия свариваемых заготовок, используя явления термического напряжения, возникающего при нагреве материалов с различными коэффициентами линейного расширения. При сварке коак-сиально собранных заготовок коэффициент линейного расширения охватывающей детали должен быть меньше коэффициента линейного расширения охватываемой детали (см. рис. 3.66, а).
Качество соединения при диффузионной сварке в вакууме определяется комплексом технологических параметров, основные из которых - температура, давление, время выдержки. Диффузионные процессы, лежащие в основе формирования сварного соединения, являются термически активируемыми, поэтому повышение температуры сварки стимулирует их развитие. Для снижения сжимающего давления и уменьшения длительности сварки температуру нагрева свариваемых деталей целесообразно устанавливать по возможности более высокой; металлы при этом обладают меньшим сопротивлением пластической деформации. Вместе с тем необходимо учитывать возможность развития процессов структурного превращения, гетеродиффузии, образования эвтектик и других процессов, приводящих к изменению физико-механических свойств свариваемых металлов.
Удельное давление влияет на скорость образования диффузионного соединения и величину накопленной деформации свариваемых заготовок. В большинстве случаев чем выше удельное давление, тем меньше время сварки и больше деформация. Так, при сварке в прессе с использованием высоких удельных давлений (до нескольких десятков мегапаскалей) время образования соединения может измеряться секундами, а деформация металла в зоне соединения десятками процентов. При сварке с использованием низких удельных давлений (десятые доли мегапаскаля) время сварки может исчисляться часами, но деформация соединяемых заготовок при этом составляет доли процента. Таким образом, задачу выбора удельного давления следует решать с учетом типа конструкций, технологической схемы и геометрических размеров соединяемых заготовок, а время сварки выбирать с учетом температуры и удельного давления. При сварке разнородных материалов увеличение длительности сварки может сопровождаться снижением механических характеристик соединения из-за развития процессов гетеродиффузии, приводящих к формированию в зоне соединения хрупких интерметаллидных фаз.
Для осуществления диффузионной сварки в настоящее время создано свыше 70 типов сварочных диффузионно-вакуумных установок. Разработка и создание установок для диффузионной сварки в настоящее время ведется в направлении унифицирования систем (вакуумной, нагрева, давления, управления) и сварочных камер. Меняя камеру в этих установках, можно значительно расширить номенклатуру свариваемых узлов. Некоторые виды конструкций, изготовленных диффузионной сваркой, приведены на рис. 3.71.
Рис. 3.71. Примеры титановых конструкций, изготовленных диффузионной сваркой
ДИФФУЗИОННАЯ СВАРКА
1. Сущность метода и основные области применения
Диффузионная сварка входит в группу способов сварки давлением, при которых соединение проходит за счет пластической деформации микронеровностей на поверхности свариваемых заготовок при температуре ниже температуры плавления. Отличительной особенностью является применение повышенных температур при сравнительно небольшой остаточной деформации. Ее технологическая характеристика была предложена Н.Ф. Казаковым и принята Международным институтом сварки в следующей формулировке: «Диффузионная сварка материалов в твердом состоянии - это способ получения неразъемного соединения, образовавшегося вследствие возникновения связей на атомарном уровне, появившихся в результате сближения контактных поверхностей за счет локальной пластической деформации при повышенной температуре, обеспечивающей взаимную диффузию в поверхностных слоях соединяемых материалов».
В практике диффузионной сварки известно применение двух технологических схем процесса, различающихся характером приложения нагрузки или напряжения, действующих в течение цикла. В одной из них используют постоянную нагрузку по величине ниже предела текучести. При этом процессы, развивающиеся в свариваемых материалах, аналогичны ползучести. Такую технологию называют диффузионной сваркой по схеме свободного деформирования. На практике подобная схема осуществима наиболее просто, поэтому очень широко распространена.
По другой схеме нагрузка и пластическая деформация обеспечиваются специальным устройством, перемещающимся в процессе сварки с контролируемой скоростью (см. рис. 1, б). Эту технологию называют диффузионной сваркой по схеме принудительного деформирования (ДСПД-процесс). Этот процесс осуществляют при напряжениях, как правило, превышающих предел текучести. Таким образом, скорость деформации £ задается приложенной нагрузкой Р и условиями, в которых она действует: прежде всего температурой Т и временем действия 1.
Промышленное применение. Технологические возможности диффузионной сварки позволяют широко использовать этот процесс в приборостроительной и электронной промышленности при создании металлокерамических и катодных узлов, вакуум-плотных соединений из разнородных материалов, полупроводниковых приборов, при производстве штампов и т.п.
Рис. 1 Схема деформирования при диффузионной сварке:
1 - система погружения; 2 -система деформирования;
Н - нагреватель; Д-детали
Диффузионная сварка находит применение для изготовления крупногабаритных заготовок деталей сложной формы, получение которых механической обработкой, методами обработки давлением или литьем невозможно или неэкономично. Особенно эффективно такое применение диффузионной сварки в опытном и мелкосерийном производстве.
Перспективно получение многослойных пустотелых конструкций типа панелей из титановых или алюминиевых сплавов с наполнителем сложной формы (гофры, соты, ребра и др.) методом совмещения диффузионной сварки и формообразования в режиме сверхпластичности.
2. Основные параметры режима
При сварке по схеме свободного деформирования основными параметрами процесса являются температура нагрева заготовок Т, 0 С; сжимающее давление р, МПа; время сварки t, мин; давление в вакуумной камере р к. Па; в случае проведения процесса в другой среде - характеристика этой среды с позиции протекания окислительно-восстановительных реакций (тип и химический состав среды, точка росы, парциальное давление кислорода). Кроме того, к важным параметрам процесса относятся подготовка поверхности под сварку: чистота поверхности, ее шероховатость и волнистость.
При ДСПД-процессе главными параметрами являются: температура Т, скорость роста нагрузки Р, скорость деформирования к, время деформирования t (или степень накопленной деформации), время выдержки в режиме релаксации t рсл. Сопротивление деформированию Р в этом случае - зависимый параметр. Его величина регистрируются непосредственно в течение всего цикла сварки. Оба параметра могут быть использованы для контроля и управления качеством соединения.
Диффузионная сварка может проводиться в вакууме, нейтральных и восстановительных газах, жидких средах. Вакуум создает наилучшие условия для защиты нагретого металла и очистки свариваемых поверхностей от загрязнения. Однако в отдельных случаях особенности материала могут налагать определенные ограничения на применение вакуума или делать его вовсе невозможным. В большинстве случаев процесс диффузионной сварки ведется при давлении в вакуумной камере p к = 10 -2 ... 10 -3 Па. Использование более высокого вакуума оправдано, когда необходимо обеспечить высокую размерную точность изделия (уменьшение остаточной деформации заготовок) за счет соответствующего снижения температуры, давления и времени. Тугоплавкие металлы удается таким образом сваривать при температурах ниже порога рекристаллизации и тем самым избегать охрупчивания материала.
На ход диффузионной сварки существенно влияет парциальный состав остаточных газов в камере. Попадание в рабочую зону паров вакуумного масла приводит к увеличению парциальных давлений газов-окислителей (С0 2 , Н 3 О) по сравнению с газами-восстановителями (СО, H 2). Специальные меры (азотные ловушки, использование безмасляных средств откачки) улучшают условия ведения диффузионной сварки, особенно при пониженных температурах.
Широко применяют в качестве защитных сред инертные (аргон, гелий) и активные газы (водород, реже углекислый газ). Состав защитного газа подбирают исходя в первую очередь из химической активности системы металл-газ в условиях сварки.
Подготовка заготовок в общем случае может складываться из механической обработки, очистки от загрязнений и нанесения подслоев. Механическая обработка обеспечивает: возможно, более плотное начальное прилегание свариваемых заготовок; удаление с поверхности загрязненного слоя; повышение размерной точности готового изделия; возможность снижения температуры, давления и времени сварки с улучшением микрогеометрии поверхности.
С повышением чистоты обработки облегчается развитие второй стадии процесса.
Очистка поверхностей от загрязнений (следов жиров, масла, полировальной пасты) может проводиться растворителями (ацетон, спирт, четыреххлористый углерод и др.), путем нагрева и выдержки в вакуумной камере. В отдельных случаях применяют отжиг заготовок в среде водорода. Положительные результаты получают при обработке в растворах кислот H 2 S0 4 , MCI с последующими промывкой и сушкой. При сварке изделий из некоторых сортов керамики после механической обработки заготовки отжигают с целью «залечивания» поверхностных дефектов. Для этого же проводят травление стекла в плавиковой кислоте.
Для выбора температуры, давления и времени нет строгих рекомендаций. Высококачественные соединения можно получать, изменяя в определенных пределах значения каждого из этих параметров с соответствующей корректировкой других. При выборе их значений необходимо учитывать особенности свариваемых материалов и требования к изделию; возможность разупрочнения из-за роста зерна, ограничения по температуре нагрева и деформации изделия и т.п.
Температуру сварки обычно назначают в пределах (0,5...0,8)Т пл, для жаропрочных сплавов - несколько выше. При соединении разнородных материалов расчет ведется по температуре плавления наиболее легкоплавкого из них. В случае появления эвтектики температуру сварки выбирают ниже температуры ее плавления.
Скорости нагрева и охлаждения зависят от источника тепла и в большинстве случаев их не регламентируют. При сварке разнородных сочетаний материалов, термический коэффициент линейного расширения которых различается более чем на 2 10 -6 град -1 , скорость охлаждения целесообразно уменьшать до 10…15 0 С/мин.
Разгерметизацию камеры при сварке деталей из черных металлов рекомендуют проводить при температуре ≤120 °С, а для цветных и активных металлов - при 60 0 С.
Время выдержки в зависимости от Т и р, допустимой остаточной деформации, чистоты обработки контактных поверхностей и деформационной способности материала может колебаться от нескольких секунд до нескольких часов (чаще 5... 10 мин).
Давление выбирают в диапазоне 0,8…0,9 предела текучести при температуре сварки. Для известных конструкционных материалов оно может изменяться в диапазоне 1 ...50 МПа. Для сварки тугоплавких и твердых материалов эти значения могут быть в несколько раз выше.
4. Технологические возможности процесса
Диффузионная сварка позволяет сваривать:
Большинство конструкционных материалов на металлической основе, ферриты, керамику, стекла, кварц, сапфир, графит, полупроводниковые материалы в однородном и разнородных сочетаниях;
Пористые, металлокерамические, композиционные материалы без нарушения их текстуры и ухудшения служебных свойств;
При использовании соответствующих барьерных покрытий и проставок - разнородные металлы и сплавы, склонные к образованию хрупких фаз, тугоплавкие металлы (вольфрам, ниобий, тантал и др.) при температурах ниже порога рекристаллизации.
Диффузионная сварка дает возможность также избежать охрупчивания металла. С использованием промежуточных проставок можно также соединять материалы с резко отличными значениями коэффициентов термического расширения.
Диффузионной сваркой можно выполнять все типы соединений при самом разнообразном конструктивном их оформлении: встык, вскос, соединять пересекающиеся стержневые элементы между собой и с плоскими или криволинейными поверхностями; сваривать заготовки любых сечений; при применении местного нагрева и вакуума - соединять заготовки неограниченной длины; сваривать пленки, фольгу толщиной в несколько микрометров и достаточно массивные детали; осуществлять сварку при практически любой разнотолщинности заготовки.
После диффузионной сварки не нужна механическая обработка сварного шва, получаемые изделия обладают высокой размерной точностью (остаточные деформации в пределах 0,1...6 %); швы имеют высокие показатели механической прочности и пластичности на уровне основного материала.
При использовании этого метода создаются хорошие гигиенические условия на производстве.
К недостаткам метода следует отнести значительную длительность процесса, сложность оборудования, определенные трудности с загрузкой заготовок и выгрузкой готовых изделий из рабочей камеры при организации непрерывного процесса изготовления сварных изделий, требования достаточно высокой точности сборки и чистоты обработки свариваемых поверхностей, необходимость контроля температуры заготовки в зоне шва. Высокие требования к качеству контактных поверхностей удорожают процесс в целом.
5. Разновидности способов сварки
Диффузионная сварка с промежуточными прокладками. Промежуточные прокладки могут быть расплавляющимися и нерасплавляюшимися. Подслои на свариваемые поверхности наносят с целью:
Увеличения прочности сцепления (сваривания);
Предотвращения появления нежелательных фаз при сварке разнородных материалов (барьерные подслои);
Интенсификации стадии объемного взаимодействия;
Облегчения установления физического контакта по всей свариваемой поверхности за счет использования подслоев из пластичных материалов;
Снижения температуры и давления при сварке и, значит, уменьшения остаточных деформаций.
В зависимости от конкретной задачи выбирают материал подслоя. Чаще всего это никель, медь, серебро, золото. Толщина подслоя порядка 2. ..7 мкм.
Для предотвращения появления нежелательных, фаз (интерметаллидов, карбидов и т.д.) или во избежание обеднения одного из свариваемых материалов каким-либо легирующим элементом наносятся более толстые покрытия, служащие барьером. Эту задачу могут выполнять и прокладки из фольги.
Материал барьерной прокладки должен выбираться так, чтобы коэффициент его диффузии в основной материал был выше, чем для элементов основного металла в прокладку.
В случае сварки материалов на основе оксидов (керамики, стекла) наносимый металлический слой подвергают термической обработке с целью его окисления или облегчения диффузии в материал заготовки. При сварке кварцевого стекла с медью на стекло наносят слой меди с последующим ее окислением при температуре 800 0 С в течение 3...5 мин до закиси. При сварке меди с оптической керамикой на основе сульфидов цинка применяют предварительное сульфидирование металла для повышения прочности сцепления.
В качестве расплавляющихся прокладок наиболее часто используют высокотемпературные припои. Их применение позволяет уменьшить давление сжатия и пластические деформации, облегчает удаление оксидных пленок, повышает эксплуатационные свойства соединений.
Диффузионная сварка с применением ударной нагрузки. Для предотвращения интерметаллидов в зоне сварного соединения помимо использования соответствующих промежуточных прокладок эффективен прием заметного сокращения времени сварки. На практике этот прием реализован так называемой «ударной сваркой в вакууме». Суть способа в том, что к локально нагретым зонам контакта детали «прикладывается» одиночный импульс силы со скоростью 1...30 м/с. В свариваемых деталях под воздействием динамической нагрузки происходят локальная пластическая деформация в зоне контакта и образование сварного соединения. Сварное соединение образуется за 1…10мс.
6. Оборудование
Наиболее широко применяют сварочные диффузионные вакуумные установки. В состав этих установок в общем случае входят рабочая вакуумная камера, механизм для создания сварочного давления, источник нагрева, вакуумная система, аппаратура управления и контроля. Конкретные установки (П-114, П-115, ДФ-101, УСДВ-630, ДСВ-901, УДС-ЗМ и др.) для диффузионной сварки могут иметь различное конструктивное оформление отдельных функциональных узлов и систем.
Рабочая вакуумная камера, в которой размещаются свариваемое изделие, нагреватели, механизм давления, выполняется обычно цилиндрической или прямоугольной формы из коррозионно-стойкой стали. Стенки водоохлаждаемые. Свариваемое изделие может располагаться на специальной опоре или в приспособлении. В большинстве случаев установка имеет одну камеру. Для увеличения производительности могут предусматриваться несколько камер с целью получения непрерывной загрузки и выгрузки заготовок и изделий (камеры шлюзования}.
Необходимая сварочная сила создается гидравлическим, пневматическим или механическим устройством. В отдельных случаях сжатие заготовок обеспечивается специальными приспособлениями, принцип действия которых основан на различии коэффициентов линейного расширения материалов свариваемых заготовок и охватывающих их элементов приспособления. Такие приспособления позволяют вести сварку в серийно выпускаемых вакуумных и водородных печах. Возможно использование «мягких» оболочек-камер. Сжатие заготовок происходит за счет перепада давлений внешней газовой среды и вакуумированного пространства. В большинстве же случаев в установках для диффузионной сварки используются гидравлические и механические системы.
Для нагрева заготовок наибольшее распространение получили индукционный, радиационный и контактный способы. Источником питания являются генераторы высокой частоты и трансформаторы. Нагрев током высокой частоты (ТВЧ) наиболее универсален и позволяет нагревать заготовки в разведенном состоянии (в отличие от контактного метода), что важно для интенсификации процесса очистки свариваемых поверхностей. Однако этот метод неприменим при сварке диэлектрических материалов: керамики, кварца, стекла. Для нагрева годятся тлеющий разряд, расфокусированный электронный луч, световое излучение.
Еще из раздела Промышленность, производство:
- Реферат: Качество продукции и организация технического контроля
Диффузионная сварка является разновидностью способов спайки металлических заготовок, которая проводиться под давлением высокой температуры методом воздействия на детали сдавливающим вакуумом. Что представляет собой данная техника, более подробно рассмотрим в этой статье.
Методы применения диффузионной сварки
Диффузионная сварка может проходить по двум технологическим режимам, что отличаются способом подачи давления на поверхность. Первым из способов является подача давления на свариваемую деталь постоянного характера, доводя процесс до предела расплавки.
Технология широко применима в связи со свободным формированием изделий. Вторым способом является задействование специального оборудования, которое имеет вращающийся вал, позволяющий создавать нагрузочное воздействие на деталь до состояния текучести.
Преимущества и недостатки
Диффузионная сварка имеет такие плюсы:
минимальная энергозатрата по сравнению с остальными инверторами;
для соединения диффузии не применяются электродная проволока и припои;
высокие показатели соединения;
возможность соединять любые геометрические элементы;
безопасный рабочий процесс.
К недостаткам относят такие особенности:
сварочный диффузионный процесс требует наличие вакуумного блока, отсутствие которого делает процесс невозможным;
необходимость предварительной зачистки поверхности болгаркой;
длительность рабочего режима.
Способы проведения сварки
Диффузионная сварка выполняется на основе прокладок, имеющих свойство плавления и неплавления. В качестве прокладок используются никель, медь, сплавы серебра и золота. На сварную зону наносится специальный подслой, который предназначен для:
повышение качества стыка;
препятствие на пути образования пористости в волокнах металла;
захвата большей площади заготовок;
контактирования с поверхностью сварного элемента;
стабилизации температурного режима без разрушения внутреннего слоя.
Диффузионные качества могут как положительно сказаться на сварном шве, так и негативно вследствие разрушительного температурного воздействия. Чтобы поддерживалась стабильная энергофаза, барьерной основой может служить толстостенная фольга. Подбирается основной материал с учетом диффузного коэффициента, который должен быть выше показателя главной заготовки. Если спаять нужно стеклянные или керамические изделия, то подслой металла накаляют до окисляющей реакции. Это поможет дальнейшему процессу соединения, где диффузия будет протекать быстрее.
Спайку изделий из меди, которым свойственно окисление, осуществляют под влиянием температуры в 800С в течение 5 минут. Для соединения керамических и медных деталей используется сульфид цинка.
Высокотемператур ные исходники позволяют уменьшить процесс сжатия и сделать проще процесс устранения оксидного покрытия. Тем самым эксплуатационные сроки значительно увеличиваются.
Диффузионная сварка методом ударной нагрузки под вакуумом применима в случае образования металлоидных пор в сварной зоне. Данный способ дает возможность контактному участку деталей предельно нагреться, после чего происходит воздействие единичного силового импульса, скорость которого равна 1-30 м/с.
При подаче динамической нагрузки на поверхность заготовок в зоне выработки тепла происходит динамическое влияние, способствующее процессу плавления. Металл в состоянии жидкости заполняет стыковочные места и производит ровный шов. Это происходит за 1-10 мс.
Технология диффузионной сварки
Диффузная сварка на практике используется по двум технологиям: первая подразумевает постоянную подачу энергоимпульса на элемент заготовки, вторая технология состоит из комбинированного соединения, в основе которой лежит пластическая деформация и сила сжатия. Скоростной режим регулируется в процессе сварки.
Диффузионная сварка состоит из такого рода последовательнос ти: сначала происходит сбор заготовочных частей оборудования, которое позволяет подать необходимую нагрузку на зону соединения. Далее части подвергаются вакуумной обработке, чтобы они легче поддавались нагреву. После того как прекратилось воздействие на металл, изделие должно оставаться в покое до полного естественного остывания.
Образование сварочного шва производится двумя способами: физическим и стадиями формирования. Первый способ осуществляется с помощью физического давления на сварную зону. Второй способ включает в себя разогрев, силу давления, процесс сжатия.
Временной режим можно выставить в зависимости от плотности сварной детали. Он может варьироваться от пары до нескольких десятков минут. Расплавка металловолокна происходит методом индукции, а на процесс может влиять электролуч, имеющий обратное сопротивление. Соединение происходит в без окислительном режиме нагрева. Для защитной функции от окислов используют вакуум, а исходные детали перед действием тщательно проходят обработку.
Cтраница 1
Вакуумная сварка обеспечивает безокислительный нагрев и применяется для соединения ответственных деталей приборов и измерительных инструментов, например для соединения твердосплавных пластин со сталью при изготовлении концевых мер длины, армированных твердым сплавом.
Для вакуумной сварки детали небольших толщин собираются плотно, без видимых зазоров IB стыках, ио не на прессовой посадке.
Интересен метод вакуумной сварки плавящимся электродом, разработанный в последнее время в МВТУ - МЭИ. При этом способе сварки горение дуги происходит в парах металла. Способ очень рационален для сварки толстостенных изделий из алюминиевых, титановых и других сплавов. Сварка в вакууме плавящимся электродом производительная, разогрев получается концентрированным, качество соединений высокое. В настоящее время уже разработаны крупногабаритные камеры для сварки этим способом.
Одной из разновидностей вакуумной сварки является диффузионная. В этом способе удачно скомбинированы вакуумирование, подогрев и обжатие деталей. При вакуумной сварке температура подогрева значительно ниже температуры плавления. Это позволяет осуществлять соединения без отрицательного термического влияния на прилегающие к шву металлы. Диффузионной сваркой соединяются различные однородные и разнородные тугоплавкие металлы, сплавы, окислы, керамика. В настоящее время производятся разносторонние разработки и исследования по улучшению оборудования для диффузионной сварки и технологических процессов соединений всевозможных материалов.
Электроды, пригодные для вакуумной сварки, должны обеспечивать получение металла шва, обладающего высокой пластичностью, очень плотного, не склонного к образованию трещин, с легко отделяемой шлаковой коркой.
Во Франции разработан метод вакуумной сварки тугоплавких и химически активных металлов потоком электронов. При этом методе поверхность металла, находящегося в вакууме, расплавляется за счет энергии, отдаваемой бомбардирующими электронами при ударах об эту поверхность. Направляя пучок электронов на место сварки, производят здесь сплавление металла свариваемых частей.
Диапазон толщин деталей, свариваемых диффузионной вакуумной сваркой, очень большой.
В особо ответственных случаях (при вакуумной сварке и др.) целесообразно удалить поверхностный слой меди на глубину 0.4 - 0.5 мм.
Больше всего в этой книге уделено места вакуумной сварке и пайке, имеющим особо важное значение в вакуумном аппаратостроении.
Для тугоплавких и весьма активных металлов может найти применение вакуумная сварка электронным лучом. Этот способ пока еще мало разработан, осуществление его встречает некоторые трудности, но, несомненно, он открывает возможность соединять некоторые трудносвариваемые материалы. Для повышения производительности сварки электронным лучом необходимо внедрение автоматизированных и механизированных процессов в производство, обеспечивающих непрерывную работу установки.
В отношении подачи кислорода также никаких особых требований для вакуумной сварки не предъявляется.
Азот дешев, но не может быть применен для вакуумной сварки стали, так как при высоких температурах в среде азота образуются нитриды железа и хрома, обладающие очень высокой твердостью и делающие сварной шов неравномерным и пористым.
Указаны условия получения 1вакуумно - плотных сварных и паяных швов, кратко описаны лучшие методы вакуумной сварки и аппаратура для нее. Приведены рецептура и способы приготовления флюсов для вакуумной пайки черных и цветных металлов.
ФЕДЕРАЛЬНОЕ АГЕНСТВО ПО ОБРАЗОВАНИЮ
ГОСУДАРСТВЕННОЕ ОБРАЗОВАТЕЛЬНОЕ УЧРЕЖДЕНИЕ
ВЫСШЕГО ПРОФЕССИОНАЛЬНОГО ОБРАЗОВАНИЯ
МОСКОВСКИЙ ГОСУДАРСТВЕННЫЙ ИНСТИТУТ РАДИОТЕХНИКИ, ЭЛЕКТРОНИКИ И АВТОМАТИКИ (ТЕХНИЧЕСКИЙ УНИВЕРСИТЕТ)
КУРСОВАЯ РАБОТА
«ТИПОВОЙ ТЕХНОЛОГИЧЕСКИЙ ПРОЦЕСС
ДИФФУЗИОННОЙ СВАРКИ В ВАКУУМЕ»
Выполнила студентка гр. ЭС-11-06
Ивлева Ю. И.
Преподаватель
Рыбников Ю.С.
Москва 2009
Введение……………………………………………………………………...стр.3
Технологическая маршрутная карта………….…………………………….стр.5
Характеристика и технические требования к исходным материалам……стр.5
Типовой технологический процесс…………………………………………стр.5
Оборудование, оснастка и инструменты…………………………………...стр.5
Контроль качества……………………………………………………………стр.5
Требования техники безопасности и промышленной санитарии…………стр.6
Приложение 1, рис.1……………….…………………………………………стр.7
Введение.
Диффузионная сварка широко применяется в машиностроении. Отличительной особенностью является применение относительно высоких температур нагрева и сравнительно низких удельных сжимающих давлений при изотермической выдержке от нескольких минут до нескольких часов.
Формирование диффузионного соединения определяется такими процессами, как взаимодействие нагретого металла с газами окружающей среды, очистка свариваемых поверхностей от оксидов, развитие высокотемпературной ползучести и рекристаллизации.
Для уменьшения скорости окисления свариваемых заготовок и создания условий очистки контактных поверхностей от оксидов при сварке могут быть применены газы – восстановители, расплавы солей, флюсы, обмазки, чаще вакуум или инертные газы.
Сближение свариваемых поверхностей происходит за счет пластической деформации микровыступов и поверхностных слоев, обусловленных приложением внешних сжимающих напряжений и нагревом металла.
В процессе деформации свариваемых поверхностей происходит их активация и при развитии физического контакта между ними реализуется их схватывание.
При диффузионной сварке одноименных металлов сварное соединение достигает равнопрочности основному материалу и том случае, когда структура зоны соединения не отличается от структуры основного материала. Для этого в зоне контакта должны образовываться общие для соединяемых зерна. Это возможно за счет миграции границ зерен, осуществляемой либо путем рекристаллизации обработки, либо путем собирательной рекристаллизации.
Соединяемые заготовки могут быть весьма различны по своей форме и иметь компактные или развитые поверхности контактирования. Геометрические размеры свариваемых деталей находятся в пределах от нескольких микрон до нескольких метров.
Диффузионная сварка - способ сварки без расплавления основного металла за счёт нагрева и сдавливания соединяемых деталей. В месте сварки деталей происходит диффузия одного металла в другой. Детали с тщательно зачищенными и пригнанными поверхностями помещают в закрытую сварочную камеру с разрежением до ~0,01-0,001 н/м 2 , т. е. до 10 -5мм рт. ст . Детали сдавливают небольшим постоянным усилием, для повышения пластичности и ускорения диффузии нагревают до 600-800°С. При нагреве в вакуумной камере происходит интенсивная очистка поверхностей от органических загрязнений и окислов. В некоторых случаях после снятия давления изделие дополнительно выдерживают при температуре сварки для более полного протекания рекристаллизационных процессов, способствующих формированию качественного соединения. Через несколько минут после окончания сварки детали охлаждается в вакууме, инертной среде или на воздухе в зависимости от типа оборудования.
В зависимости от напряжений, вызывающих деформацию металла в зоне контакта и определяющих процесс формирования диффузионного соединения различают сварку с высокоинтенсивным и низкоинтенсивным силовым воздействием. В первом случае сварочное давление создают с помощью пресса, снабженного вакуумной камерой и нагревательным устройством. Но такие установки позволяют сваривать детали ограниченных размеров (до 80 мм).
Для исключения возможности потери устойчивости свариваемых элементов, передачи давления в зону сварки и создания условий локально-направленной деформации свариваемого металла в зоне стыка диффузионную сварку осуществляют в приспособлениях с использованием для заполнения межреберных пространств технологических вкладышей и блоков, которые после сварки убирают химтравлением или демонтируют.
Качество соединения зависит от температуры, давления, времени выдержки.
Диффузионные процессы, формирующие сварочное соединение, являются термически активируемыми, поэтому повышение температуры сварки стимулирует их развитие.
При сварке разнородных материалов увеличение длительности сварки может сопровождаться снижением механических характеристик соединения из-за развития процессов гетеродиффузии.
В настоящее время создано свыше 70 типов сварочных диффузионно-вакуумных установок, меняя камеру в этих установках, можно значительно расширить номенклатуру свариваемых узлов.
Параметры технологии процесса диффузионной сварки:
- температура сварки до 0,7-0,8 Т плавления;
- удельное усилие сжатия до 1-2 кгс/мм 2 ;
- время нагрева деталей до температуры сварки;
- время охлаждения изделия;
- степень разряжения в вакуумной камере от 0,1 до 5·10 -3 мм рт ст
Преимущества процесса сварки:
- возможность получения соединений однородных и разнородных материалов;
- малые деформации свариваемых деталей (5-7%);
- безотходная технология;
- экологически чистый процесс работы машин для диффузионной сварки;
- отсутствуют расходные материалы (дорогостоящие припои, флюсы, пасты);
- возможность получения соединения с большой площадью сварной зоны (ограничивается усилием привода сжатия установки);
- единственно надежные способ получения гибких медных шин, связей, компенсаторов путем омоноличивания мест под болтовое соединение;
- замена пайки на диффузионную сварку экономит дорогостоящие припои, значительно улучшает качество соединений: обеспечивает стабильный электрический контакт, переходное сопротивление соединения отсутствует, прочность, термическая и коррозионная стойкость увеличивается, внешний вид изделия безупречный, отсутствует окалина и следы побежалости;
- диффузионная сварка меди с серебряной и никелевой фольгой заменяет гальванические покрытия
Области применения:
- изделия низковольтной и высоковольтной аппаратуры (например, контакторы электромагнитные; разъединители; масляные, вакуумные и автоматические выключатели; контакты; пускатели; комплектные трансформаторные подстанции КТП; высоковольтные камеры КСО для комплектно-распределительных устройств КРУ и т.д.);
- шинопроводы, гибкие шины, связи, компенсаторы, токоподводы;
- оконцевание проводов и кабелей (замена кабельных наконечников);
- композиционные материалы с заданными свойствами;
- элементы скважинных насосов (биметаллическое седло и шток клапана);
- трансформаторы и электрические машины.
Технологическая маршрутная карта.
Настоящий типовой технологический процесс дает описание формирования диффузионного соединения однородных материалов и оборудования и оборудования для его реализации.
1. Характеристика и технические требования к исходным материалам.
1.1. Отличительная особенность диффузионной сварки от других способов сварки давлением - относительно высокие температуры нагрева (0,5-0,7 Т пл) и сравнительно низкие удельные сжимающие давления (0,5-0 МПа) при изотермической выдержке от нескольких минут до нескольких часов.
2. Типовой технологический процесс сварки однородных материалов из меди.
2.0. Технологическая схема диффузионной сварки дана в приложении 1.
2.1. Последовательность технологического процесса:
2.1.1. Предварительная подготовка поверхности:
1. обезжиривание трихлорэтиленом;
2. промывка горячей и дистиллированной водой;
2.1.2. Установка вручную свариваемых деталей в вакуумную камеру, закрытие дверцы камеры.
2.1.3. Откачка воздуха из камеры.
2.1.4. Сближение свариваемых поверхностей.
2.1.5. Нагрев деталей до температуры сварки ≈600-800 ˚С
2.1.6. Подача сжимающего давления 1-2 кгс/мм² на заданный период времени 3-15 мин.
2.1.7. Охлаждение соединения в вакууме.
2.1.8. Напуск воздуха в камеру.
3. Оборудование, оснастка и инструменты.
3.1. Специализированные установки и машины диффузионной сварки состоят из источника питания; вакуумной и электрической систем; системы охлаждения вакуумной камеры, свариваемых деталей и электродов; привода усилия сжатия; гидравлической или пневматической системы привода усилия сжатия. Электроконтактный нагрев деталей в процессе сварки осуществляется переменным или постоянным током. Система управления установкой выполняется на базе релейной или микропроцессорной техники.
4. Контроль качества.
4.1. Определение визуального соответствия на внешний вид. 4.2. Определение прочности шва на разрыв с помощью разрывной машины. 4.3. Определение на вакуумную плотность (герметичность) гелиевым течеискателем.
5. Требования техники безопасности и промышленной санитарии.
5.1. При работе за специализированными установками и вакуумными печами диффузионной сварки необходимо руководствоваться следующими нормативными материалами:
А) /«Производственные здания промышленных предприятий. Нормы проектирования»/ СНиП, П-М, 2-74/; Б) /«Противопожарные требования. Основные положения проектирования»/ СНиП, П-Е, 7-74/; В) /«Отопление, вентиляция и кондиционирование воздуха. Нормы проектирования»/ СНиП, П-Е, 7-74/; Г) /«Внутренний водопровод производственных и вспомогательных зданий промышленных предприятий. Нормы проектирования»/ СНиП, П-Г, 2-74/.
5.2. Меры безопасности при эксплуатации и техническом обслуживании линии. 5.2.1. Эксплуатация прессов, работающих под давлением, разрешается персоналу, имеющему удостоверения о прохождении «Правил эксплуатации прессов, работающих под давлением». 5.2.2. Все оборудование линии должно иметь надежное заземление и в процессе эксплуатации регулярно проверяться. 5.2.3. Запрещается находиться в зоне вакуумной и электрической систем без предохранительной одежды, очков, респиратора. 5.2.4. Перед пуском машин в эксплуатацию каждый раз необходимо производить проверку работы системы охлаждения вакуумной камеры, свариваемых деталей и электродов, привода усилия сжатия, гидравлической и пневмонической системы сжатия. 5.2.5. Перед пультом электроуправления должны быть диэлектрические коврики. 5.2.6. При работе системы шкафы пультов управления должны быть закрыты на ключ. 5.2.7. Электрическую систему обязательно отключать при неработающих машинах. 5.2.8. При работе с трибоэлектрическим зарядным устройством генерируемый постоянный ток необходимо отводить на землю.
Приложение 1.
Технологическая схема диффузионной сварки: а – требуемая конструкция; б – заготовки для сварки; в – сборка; г – сварка; д – готовая конструкция; 1 – несущая обшивка; 2 – готовый заполнитель; 3 – технологические листы; 4 – мембрана.
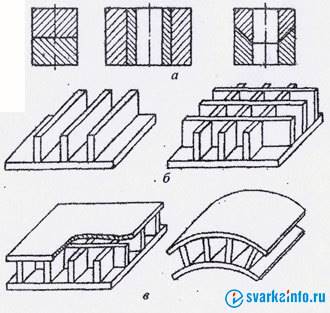
Рис.1. Некоторые типы конструкций, получаемые диффузионной сваркой.