Акт освидетельствования котла. Подготовка оборудования к ремонту. Экспертная оценка состояния помещения
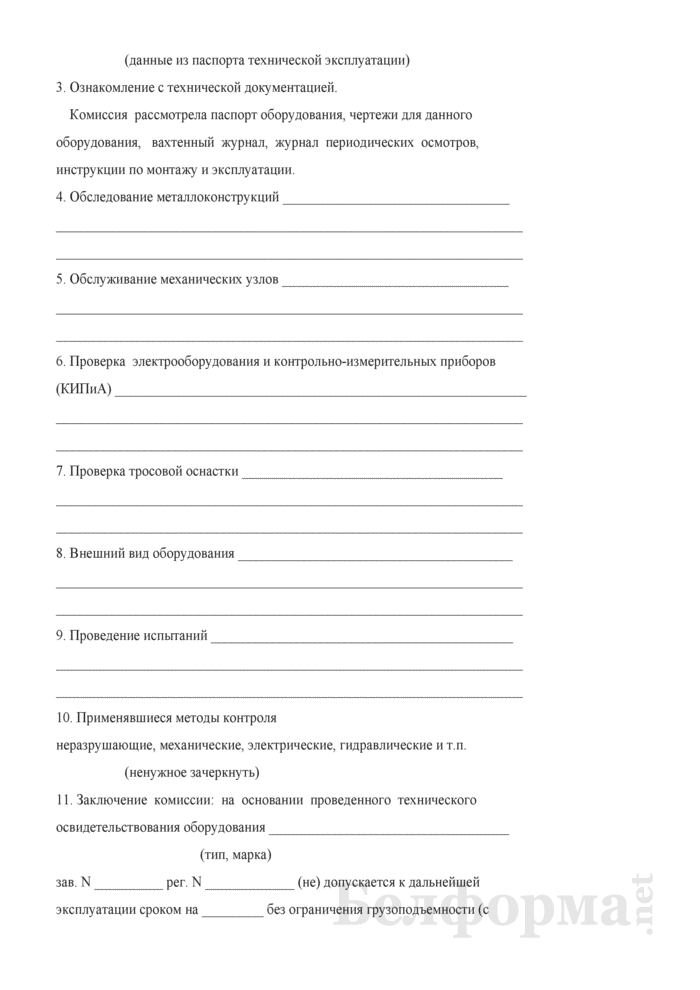
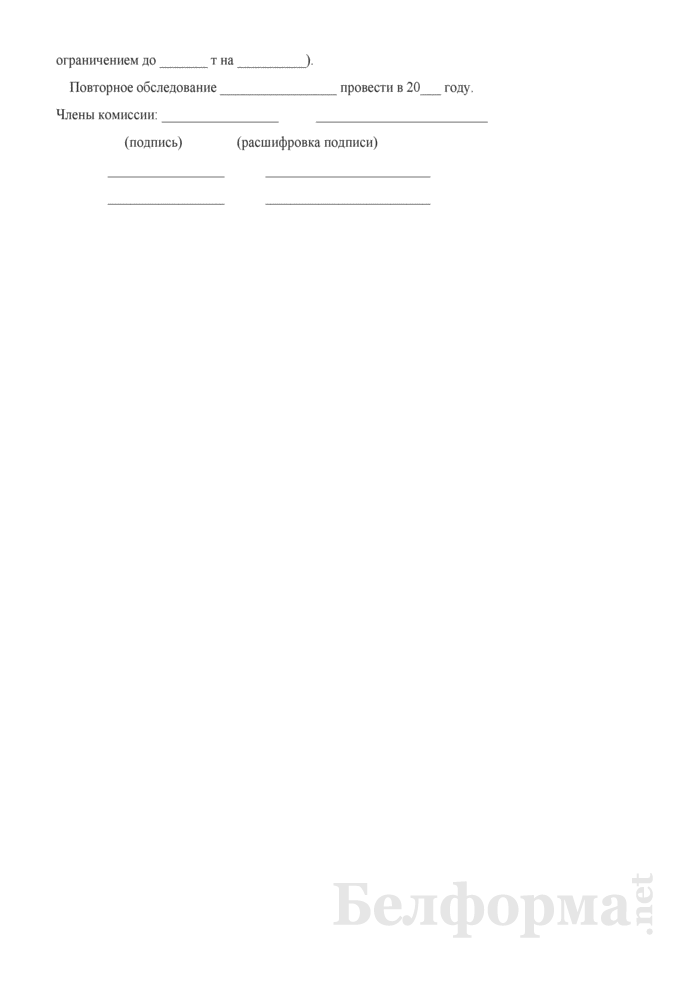
Текст документа:
Утвержден постановлением Минприроды, МЧС от 05.07.2007 N 71/64
АКТ N ___ ТЕХНИЧЕСКОГО ОСВИДЕТЕЛЬСТВОВАНИЯ оборудования _______________________________ зав. N _______________ рег. N _________________ "__" _______________ 20__ г. Комиссия в составе: ________________________________________________ ____________________________________________________________________ ____________________________________________________________________ действующая на основании приказа N __________ от "___" _____________ 20__ г. ____________________________________________________________ (наименование организации) провела техническое освидетельствование оборудования _______________ (тип, марка) ______________________ зав. N _______________ рег. N _______________ отработавшего моторесурс (нормы амортизационных отчислений), с целью определения возможности его дальнейшей эксплуатации. 1. Основание для проведения технического освидетельствования. Техническое освидетельствование оборудования __________________ ______________________________________ проводилось на основании технических условий, технологии, инструкции, положения, методики (ненужное зачеркнуть) 2. Данные паспорта технической эксплуатации оборудования. Оборудование изготовлено в _____ году, завод-изготовитель _____ _______________________________________________________________ В настоящее время оборудование ________________________________ ____________________ (не) работает _________________________________ (указать комплектность или модернизацию) Режимы работы _________________________________________________ (сколько машино-часов отработано до настоящего времени (данные из паспорта технической эксплуатации) 3. Ознакомление с технической документацией. Комиссия рассмотрела паспорт оборудования, чертежи для данного оборудования, вахтенный журнал, журнал периодических осмотров, инструкции по монтажу и эксплуатации. 4. Обследование металлоконструкций _________________________________ ____________________________________________________________________ ____________________________________________________________________ 5. Обслуживание механических узлов _________________________________ ____________________________________________________________________ ____________________________________________________________________ 6. Проверка электрооборудования и контрольно-измерительных приборов (КИПиА) ____________________________________________________________ ____________________________________________________________________ ____________________________________________________________________ 7. Проверка тросовой оснастки ______________________________________ ____________________________________________________________________ ____________________________________________________________________ 8. Внешний вид оборудования ________________________________________ ____________________________________________________________________ ____________________________________________________________________ 9. Проведение испытаний ____________________________________________ ____________________________________________________________________ ____________________________________________________________________ 10. Применявшиеся методы контроля неразрушающие, механические, электрические, гидравлические и т.п. (ненужное зачеркнуть) 11. Заключение комиссии: на основании проведенного технического освидетельствования оборудования ___________________________________ (тип, марка) зав. N __________ рег. N _____________ (не) допускается к дальнейшей эксплуатации сроком на _________ без ограничения грузоподъемности (с ограничением до _______ т на __________). Повторное обследование _________________ провести в 20___ году. Члены комиссии: _________________ _________________________ (подпись) (расшифровка подписи) _________________ ________________________ _________________ ________________________
Приложения к документу:
- (Adobe Reader)
Какие документы есть еще:
Что еще скачать по теме «Акт»:
-
Ни для кого не секрет, что юридически грамотный подход к составлению договора или контракта является гарантией успешности сделки, ее прозрачности и безопасности для контрагентов. Правоотношения в сфере найма не исключение. -
В процессе хозяйственной деятельности многих фирм наиболее часто используется договор поставки. Казалось бы, этот простой, по своей сути, документ должен быть абсолютно понятным и однозначным.
Техническое освидетельствование котла выполняется с целью установления исправности котла и пригодности его к дальнейшей работе. Оно состоит из наружного, внутреннего осмотров и гидравлического испытания.
Техническому освидетельствованию должен подвергаться каждый котел до пуска в работу, периодически во время работы и в необходимых случаях - внеочередному освидетельствованию. Техническое освидетельствование выполняет специализированная организация.
Осмотры котла проводятся с целью проверки правильности установки и оборудования котла в соответствие с регистрационными документами и на отсутствие повреждений (первичное освидетельствование) или на пригодность его к дальнейшей работе (периодическое или внеочередное освидетельствования). При осмотрах обращается внимание на наличие трещин, надрывов, отдулин, выпучин, коррозийных повреждений, следов пропаривания и пропусков в сварных и вальцовочных соединениях, а также повреждений обмуровки, могущих вызвать опасность перегрева металла элементов котла.
Ежедневный осмотр проводится при приеме смены в течение, примерно, 20-30 мин;
Ежемесячный осмотр проводится в течение 2-3 суток;
Полугодовые осмотры проводятся в течение 7-8 суток;
Текущий ремонт котлов типа ДКВР, ДЕ, ПТВМ, МЗК и др. проводится один раз в год;
Капитальный ремонт этих же котлов проводится один раз в 3,5 - 4 года.
Более подробно сроки проведения капремонта котлов в зависимости от способа сжигания топлива, мощности котла, а также сроки капремонта сборочных единиц котлов даны в ГОСТ 24005-80 «Котлы паровые стационарные с естественной циркуляцией. Общие технические требования».
Для другого оборудования ремонты проводятся в другие сроки. Например, для насосов текущий ремонт рекомендуется проводить один раз в 6 месяцев, а капитальный ремонт один раз в 6 лет.
Подготовка оборудования к ремонту.
Подготовка оборудования к ремонту выполняется согласно требованиям РД-69-94 «Типовые технические условия на ремонт паровых и водогрейных котлов промышленной энергетики».
Объем ремонтных работ определяется владельцем котла по результатам технического освидетельствования и диагностирования. До начала работ ремонтная организация разрабатывает технологическую документацию на ремонт, включая подготовку места ремонта под сварку или наплавку. Ответственность за полноту и качество выполненных работ несет организация или лицо, проводившие ремонт.
Ремонт котла выполняется специализированной организацией, имеющей лицензию Госгортехнадзора на проведение данного вида работ. К выполнению работ допускаются аттестованные сварщики, аттестованные специалисты неразрушающего контроля и слесари с разрядом не ниже четвертого, имеющие практические навыки по ремонту котлов.
До начала ремонта на каждый котел составляется следующая документация:
Акт о техническом состоянии котла до ремонта;
Проект организации работ и технологические указания по проведению сварочных работ;
Спецификация на оборудование, запасные элементы, инструмент, оснастку, такелажные приспособления .
Подробное описание ремонтных работ должно быть зафиксировано в ремонтном журнале. В частности, в журнал записываются сведения об объеме выполненных работ по чистке и замене элементов котла, а также сведения о способах и размерах выборки недопустимых дефектов (коррозионных поражений, трещин и т.п.), примененных материалах и электродах, технологии сварки и сведения о сварщиках, о методах и результатах контроля.
Организация, выполнившая ремонт, оформляет и представляет заказчику в сброшюрованном виде следующую техническую документацию:
Ремонтные формуляры;
Акты на заварку контрольных сварных соединений или на вырезку производственных сварных стыков;
Протоколы механических испытаний и металлографических исследований образцов из контрольных сварных соединений;
Сертификаты на сварочные материалы, трубы, лист, штуцеры, фланцы, фасонные детали, арматуру, крепежные изделия;
Протокол прогонки шара через трубы;
Копии удостоверения сварщиков.
При ремонте барабанов котлов с применением сварки дополнительно оформляется следующая техническая документация:
Акты осмотра котла до и после ремонта;
Ремонтный формуляр барабана (в нем приводится развертка барабана, на которой наносятся расположение и номера трубных отверстий и штуцеров; расположение и номера швов барабана, обнаруженных дефектов и выборок и др. Кроме того, дается таблица о сварке)
Ремонтный формуляр трубных отверстий и штуцеров;
Технология на выполнение ремонта;
Акт на замену штуцеров;
Заключения по результатам ультразвукового, магнитопорошкового контроля и просвечивания на отсутствие дефектов после ремонта;
Заключения по результатам контроля наплавленных участков, выполненного ультразвуковым методом после гидравлического испытания;
Акт проверки технологических свойств электродов.
Допуск людей для производства ремонта внутри котла должен производиться только по письменному разрешению, называемому нарядом - допуском.
Основные технологические процессы ремонта котлов.
Ремонту котлов предшествует очистка их от наружных и внутренних загрязнений.
Наружная чистка котлов от загрязнений заключается в удалении с поверхностей нагрева, стен топки и газоходов скопившихся отложений золы, сажи, шлака, остатков несгоревшего топлива, а также ржавчины и окалины. Для очистки используются резаки, стальные метла, щетки, банники, скребки и др. инструмент, а также обдувка сжатым воздухом. В некоторых случаях применяется обмывка труб струей воды с обязательной последующей обсушкой.
Внутренняя очистка котла направлена на удаление с внутренних поверхностей барабанов, труб, коллекторов, труб отложений накипи, шлама и солей. Первоначально часть отложений удаляется струей горячей воды, которая их частично растворяет и вымывает. Оставшиеся отложения удаляются механическим или химическими способами.
Механическая чистка производится с помощью специального инструмента, такого как металлические щетки, ерши, банники, шарошечные головки (шарошки) и др.
Для очистки кипятильных труб широко применяют шарошки, которые приводятся в действие с помощью электродвигателя с гибким шлангом. Шарошка имеет форму шестерни, которая своими зубьями удаляет накипь. Обычно используется от пяти до пятнадцати шарошек (шестерен), расположенных симметрично по кругу в головке чистящего прибора и соединенных с осью головки.
При вращении оси шарошки под действием центробежных сил прижимаются к поверхности накипи и счищают ее. После применения шарошек каждая труба очищается пыжом из пакли или ветоши и продувается сжатым воздухом. Чтобы удостовериться в проходимости трубы, через нее пропускают калиброванный стальной шарик на тросе.
Для облегчения механической чистки перед ее выполнением производится частичное растворение, а в основном размягчение накипи щелочением котла. При щелочении в котловую воду вводят едкий натр NаОН, кальцинированную соду Na 2 СО 3 или тринатрийфосфат Nа 3 РО 4 . В зависимости от состава накипи и ее толщины реагенты вводятся, ориентировочно, в следующем количестве: сода - 10-20 кг, едкий натр и тринатрийфосфат - по 3-6 кг на 1 м 3 водяного объема котла.
При щелочении вода в котле прогревается паром от других котлов или слабым огневым прогревом без подъема давления или с подъемом давления пара. Продолжительность щелочения составляет 30-60 ч. После щелочения раствор сливается из котла, а котел тщательно промывается горячей водой. После этого сразу приступают к механической чистке. Обычно щелочение выполняется в строгом соответствии с требованиями инструкции по щелочению котла, которая разработана заводом - изготовителем котла. Щелочение применяется также и для чистки котла от ржавчины и масел после его монтажа.
Кислотные промывки котлов позволяют полностью растворить накипь вывести ее из котла. Раствор кислоты способен проникнуть в те загрязненные поверхности нагрева, которые обычно недоступны для механической чистки.
Чаще всего для растворения накипи используется соляная кислота, соли которой имеют высокую растворимость в воде. Промывку ведут 4-7 % раствором кислоты, подогретым до 50-65 0 С. Котел заполняется раствором полностью. С помощью промывочного бака и насоса организуется циркуляция раствора через котел продолжительностью 6-18 ч. Для предотвращения коррозии металла в раствор кислоты вводятся ингибиторы коррозии, например, марки ПБ - 5, уротропин и др. По окончании промывки для нейтрализации остатков кислоты проводится щелочение котла.
Вместо соляной кислоты химическая чистка котла может производиться менее агрессивными органическими кислотами и комплексонами.
Из органических кислот (лимонная, муравьиная, адипиновая) наиболее широко используется лимонная кислота. Концентрация кислоты в растворе должна быть в пределах 1-3 % (рН не более 4,5), скорость циркуляции раствора в котле от 0,5 до 1,8 м/с, а температура раствора 95-105 0 С. Продолжительность химической чистки составляет 3-4 ч. Отработавший раствор вытесняется из котла горячей водой.
Из комплексонов наиболее широко применяется трилон - Б, который является натриевой солью этилендиаминтетрауксусной кислоты (ЭДТА). При концентрации раствора 0,5-1 % и скорости циркуляции 0,5-1 м/с продолжительность чистки составляет 4-8 ч. Температура раствора 100 0 С.
Возможность применения реагентов для химической чистки устанавливает завод - изготовитель котла.
Ремонт поверхностей нагрева котлов.
Небольшие коррозионные и механические повреждения барабанов, коллекторов, корпусов котлов, жаровых труб и штуцеров устраняются наплавкой или заваривание, а значительные дефектные участки вырезаются и заменяются новыми.
Язвины в барабанах глубиной до 2-3 мм после разделки заполняются раствором цемента с растолченным стеклом. Повреждения длиннее 3см и с глубиной более 2-3 мм заплавляются металлом с помощью электродуговой сварки. Однако наплавление возможно только в том случае, если после разделки повреждения толщина стенки в месте выборке более 3 мм.
Трещины глубиной до 1/3 толщины стенки барабана ремонтируются как поверхностные, а более глубокие - как сквозные. Границы трещин определяются магнитной или цветной дефектоскопией и фиксируются кернением. Для предупреждения развития трещин в длину на расстоянии 10-30 мм от намеченных границ производят сверления диаметром не менее 4-5 мм.
Трещины глубиной более1/3 толщины стенки разделываются насквозь. Кромки трещины разделывают зубилом в виде канавки чашеобразной формы, после чего отверстия и канавки заплавляют электросваркой. Наплавка должна выходить за пределы участка разделки на 5-8 мм с каждой стороны с усилением (увеличение толщины) не менее 2 мм. Усиление удаляется зашлифовкой заподлицо с основным металлом.
Более глубокие разъедания на значительной поверхности устраняются вырезкой дефектных участков и вваркой заплат, заменой обечаек, штуцеров или других элементов. Отверстия под заплату должна быть больше зоны поврежденного участка на 20-50 мм в обе стороны и выполняться газовой или пламенной сваркой. Форма вырезки для заплаты должна быть овальной или прямоугольной с плавным скруглением углов радиусом не менее 100мм. Нужную кривизну заплате придают вальцовкой.
Дефектные участки труб или сами трубы удаляются газовой, пламенной и механической резкой. Вальцованные трубы разрешается удалять из барабана выбиванием, сберегая при этом гнезда от повреждений.
Покоробленные экранные и кипятильные трубы подвергают подгибке или рихтовке, если их погнутость или смещение выходит за пределы допускаемых отклонений
Неплотности в сварных соединениях труб устраняются разделкой дефектных участков до здорового металла с последующей заваркой. Форма выборки в поперечном сечении должна иметь чашеобразную форму с углом скоса кромок 12-15 0 , а ширина разделки шва должна быть на 1-1,5 мм больше ширины шва. Перед исправлением стыков с трещинами по концам трещины выполняются сверления диаметром 2-3 мм, а дефектный металл удаляется.
Дефектные вальцовочные соединения устраняются заменой дефектного конца трубы на новый или всей трубы с последующей развальцовкой. Подготовленные к вальцовке концы труб должны быть зачищены до металлического блеска на длину 50-80 мм.
При аварийных ремонтах дефектные трубы удаляются, а вместо их в местах крепления устанавливаются заглушки. При разрыве чугунных труб экономайзера их заменяют новыми или выключают, переставляя калачи. Возможна установки внутри чугунной трубы стальной трубы с разбортовкой ее концов и зажимом их калачами.
В.А. Афанасьев, директор по научной работе, НИИР «Сириус»;
Н.Д. Денисов-Винский, начальник отдела энергетических обследований,
ООО «Промтехэкспертиза», г. Москва
Для того чтобы разработать перечь типовых, общедоступных мероприятий по энергосбережению и провести их стоимостную оценку, необходимо иметь наиболее качественную и полную картину работы оборудования котельной, в частности, работы котлоагрегатов. Энергетическое обследование котлоагрегатов в основном сводится к составлению теплового баланса и определению их КПД. Первая сложность, с которой может столкнуться энергоаудитор, - это отсутствие счетчика природного газа на каждый котел и, вследствие этого, отсутствие данных по потреблению природного газа каждым котлоагрегатом. В такой ситуации составление теплового баланса котельного агрегата при его параллельной работе с другими котлами становится затруднительным. Необходимо ответить на вопрос: как определить количество газа, потребленное каждым котлом при наличии только общего расходомера?
Основным документом, определяющим порядок эксплуатации котлоагрегата, является режимная карта, которая составляется организацией, имеющей на то полномочия, после проведения режимно-наладочных испытаний. В соответствии с «Правилами технической эксплуатации тепловых энергоустановок» периодичность проведения таких испытаний для газовых котельных составляет три года. В табл. 1 в качестве примера представлена режимная карта парового котла ДКВр-6,5/13, установленного в одной из котельных, где проводилось энергетическое обследование.
В режимной карте котла приводятся значения основных параметров котлоагрегата для работы на различных уровнях мощности при максимальной эффективности. Для того, чтобы определить КПД котлоагрегата при его работе на определенной мощности (т.е. с определенным расходом топлива), можно воспользоваться данными режимной карты. Для удобства следует найти функциональную зависимость между расходом топлива и КПД котлоагрегата (рис. 1). Если организован периодический (с периодом, например, 1 ч) учет потребляемого газа, то вопрос определения КПД котельного агрегата решен.
Приведенные рассуждения относятся к одному котлу. В котельной же устанавливается несколько котлоагрегатов (как минимум два). При наличии расходомера для каждого котла (что бывает очень и очень редко) вопрос решается, как и для одного котла. При наличии же одного общего расходомера задача определения КПД для каждого котельного агрегата может быть решена при применении данных давления газа перед горелками котельного агрегата.
Суть методики заключается в определении доли потребления природного газа каждым котлом за заданный промежуток времени согласно данным режимной карты и суточной ведомости котлов при их параллельной работе и последующем расчете количества природного газа, фактически потребленного каждым котлом за тот же промежуток времени.
По данным, приведенным в режимной карте котла, необходимо найти функциональную зависимость. Для котла ДКВр-6,5/13 она представлена на рис. 2 и описывается следующим уравнением:
G(p)=62,709.p 0 , 5052 , где G - расход газа, м 3 /ч; p - давление газа перед горелками, кгс/м 2 .
Следующим шагом к определению доли потребления природного газа каждым котлом за заданный промежуток времени является вычисление среднего значения давления газа перед горелкой согласно суточным ведомостям работы котлов. Здесь следует ввести основное ограничение описываемой методики, которое заключается в том, что все приведенные выводы справедливы для котлов, у которых режимные карты в первом приближении совпадают.
В табл. 2 приведены данные из суточных ведомостей двух параллельно работающих котлов ДКВр-6,5/13. Среднее значение давления за указанный промежуток времени для первого котла составляет 73,9 кгс/м 2 , для второго - 86,9 кгс/м 2 . Согласно этим величинам и представленному выше уравнению можно найти средний удельный расход природного газа для каждого котла: 551,27 м 3 /ч для первого котла; 598,3 м 3 /ч для второго котла. На основании полученных данных можно определить долевое потребление природного газа первым и вторым котлом соответственно:
g 1 =551,27/(551,27+598,3)=0,4795;
g 2 =598,3/(551,27+598,3)=0,5205.
Таким образом, согласно вычислениям, первый котел потребил 47,95%, а второй - 52,05% общего объема природного газа, израсходованного котельной (по фактическим данным счетчика газа) за период времени, указанный в табл. 2. Для рассматриваемой котельной при работе двух котлов в параллельном режиме за 10 ч было потреблено 10114 м 3 природного газа, следовательно, первый котел потребил за этот промежуток времени 4849,6 м 3 природного газа, а второй - 5264,3 м 3 .
В результате, зная какое количество теплоты было получено при работе каждого котла за заданный промежуток времени (по данным приборов учета тепловой энергии), а также зная теплотворную способность природного газа, можно определить средний КПД каждого котла, соответствующий рассматриваемому промежутку времени. Также определить КПД можно, воспользовавшись зависимостью, указанной выше (рис. 2), на основании данных среднего расхода газа (484,96 и 526,43 м 3 /ч для первого и второго котла соответственно). Таким образом, для первого котла искомый КПД в рассматриваемый период равен 89,7%, а для второго котла - 90,5%.
После определения КПД котлов и составления теплового баланса котельной становится возможна оценка эффективности использования топливно-энергетических ресурсов и, в дальнейшем, осуществление энергосберегающих мероприятий.
Техническое обследование котельной , также называемое освидетельствованием или аудитом, проводится для проверки технического состояния котельной и её соответствия правилам промышленной эксплуатации. После обследования котельной заключается резолюция о возможности её дальнейшего использования.
Ни для кого не секрет, что котельная установка входит в число самых комплексных объектов на производстве или в жилом секторе, от бесперебойной работы которой зависит как комфорт жильцов / сотрудников, так и эффективность предприятия. Именно поэтому своевременное обследование котельной настолько важно: оно позволяет вычислить возможные слабые места в работе оборудования, вовремя заметить и заменить изношенные детали, а также предотвратить аварийную ситуацию.
Во время обследования проверке подвергаются:
- котельное оборудование , вспомогательные и дополнительные устройства;
- фундаменты здания котельной;
- несущие конструкции здания котельной.
Котельная обследуется комплексно, что позволяет оценить работу каждого из её элементов в связке. Также после проведённого обследования возможно составить перечень рекомендаций, которые приведут к увеличению срока службы котельной и помогут устранить даже минимальные неполадки.
Помимо технического обследования котельной существует ещё и энергетическое, в ходе которого оцениваются энергетические возможности котельных установок с целью оптимизировать их работу, повысить эффективность и экономичность.
Как правила, любые работы по обследованию котельных включают в себя несколько этапов :
- исследование документации котельной;
- визуальный осмотр котельного оборудования и здания котельной;
- анализ полученных данных;
- составление отчётов и рекомендаций с занесением информации в документацию.
Компания «Альянс-Тепло» предлагает Вам свои услуги по обследованию котельных установок любого вида. Располагая значительным опытом работы с котельными, мы готовы в максимально короткий срок составить грамотные отчёты и рекомендации по результатам обследования, выявить возможные неполадки, которые в дальнейшем грозили бы работоспособности котельной установки.
Кроме того, мы предлагаем свои услуги по проектированию котельной , подбору оборудования, сборке и перевозке котельных разных типов на различных видах топлива. Мы подберём ту котельную установку, которая будет работать эффективно и экономично индивидуально на Вашем предприятии.
От правильной котельной во многом зависит успех производства и удобство жителей. Доверьте работу с котельным оборудованием профессионалам!
Вас также может заинтересовать
В северном исполнении проектирование и изготовление блочно-модульных котельных имеет свои особенности, которые обусловлены невероятно суровыми климатическими условиями Севера. Особенности проектирования и строительства котельных для северной строительно-климатической зоны сформулированы в Разделе 19 СП 89.13330.2012: «Дополнительные требования к строительству в особых природных условиях. Строительство в Северной строительно-климатической зоне и в районах вечной мерзлоты».
1. Характеристика объекта.
Котельная представляет собой отопительную котельную типа КГ-4 с закрытой схемой теплоснабжения на три котла ДКВР-4-13, основное топливо - газ. Здание одноэтажное промышленное, без подвала и чердака. Здание имеет прямоугольную в плане конфигурацию, общие размеры составляют 30,0 х 18,0 м, состоит из одноэтажного двухсветного котельного зала и двухэтажной части подсобных помещений: I этаж - трансформаторная подстанция, механическая мастерская, санитарные узлы; II этаж - лаборатория химводоподготовки, мастерская КИП, комната начальника, контора и душевые.
1.1. выполнены из глиняного обыкновенного полнотелого кирпича марки «75» на растворе марки «25».
Вертикальные плоскости стен, соприкасающиеся с грунтом имеют двухслойную битумную гидроизоляцию.
1.2. Фундаменты:
1.3. Покрытие котельного зала выполнено сборными железобетонными двухскатными балками типа 1Б4-18-2, которые опираются на железобетонные колонны каркаса. По балкам смонтированы крупнопанельные плиты ПНКЛ-3 размером 3,0 х 6,0 м.
1.4. Кровля здания - мягкая рулонная из 3-х слоев рубероида на битумной мастике, утеплитель - пенобетон.
1.5. Подпольные каналы :
- основание из бетона М75;
- стенки - кирпич глиняный обыкновенный марки «100».
1.6. Дымовая труба:
- фундамент из железобетона марки М150;
- ствол трубы из кирпича глиняного обыкновенного пластического прессования.
Строительное обследование котельной
Диагностическое обследование проводилось в присутствии представителей Заказчика.
На экспертизу были представлены документы:
- - проектная документация - на 24 (двадцати четырех) листах.
На основании Договора экспертом была произведена визуальная и визуально-инструментальная экспертиза объекта, в соответствии с требованиями СП 13-102-2003 «Правила обследования несущих строительных конструкций зданий и сооружений». Произведены замеры геометрических характеристик в соответствии с ГОСТ 26433.0-95 «Система обеспечения точности геометрических параметров в строительстве». Правила выполнения измерений. Общие положения.
Обследование строительных конструкций зданий и сооружений проводится, как правило, в три связанных между собой этапа:
- - подготовка к проведению обследования;
- - предварительное (визуальное) обследование;
- - детальное (инструментальное) обследование.
В соответствии с требованиями СП 13-102-2003 п. 6.1 Подготовка к проведению обследований предусматривает ознакомление с объектом обследования, проектной и исполнительной документацией на конструкции и строительство сооружения, с документацией по эксплуатации и имевшим место ремонтам и реконструкции, с результатами предыдущих обследований.
Экспертом произведен внешний осмотр строения, с выборочным фиксированием на цифровую камеру, что соответствует требованиям СП 13-102-2003 п. 7.2 Основой предварительного обследования является осмотр здания или сооружения и отдельных конструкций с применением измерительных инструментов и приборов (бинокли, фотоаппараты, рулетки, штангенциркули, щупы и прочее).
Обмерные работы производились в соответствии с требованиями СП 13-102-2003 п.8.2.1 Целью обмерных работ является уточнение фактических геометрических параметров строительных конструкций и их элементов, определение их соответствия проекту или отклонение от него. Инструментальными измерениями уточняют пролеты конструкций, их расположение и шаг в плане, размеры поперечных сечений, высоту помещений, отметки характерных узлов, расстояния между узлами и т.д.
Специалистом произведена диагностическая экспертиза объекта с определением технического состояния здания в соответствии с нормативными требованиями.
В результате диагностического обследования объекта установлено следующее.
2.1. Основание и фундаменты
- фундаменты несущих колонн каркаса - монолитный железобетон;
- фундаменты ограждающих конструкций - сборные железобетонные балки;
- фундаменты внутренних стен - фундаментные блоки стеновые (ФБС);
- фундаменты под котлы - обвязка из монолитного железобетона и кирпичной кладки.
- Сколов, растрескиваний и разрушений не обнаружено.
2.1.1. Проведение измерений технических параметров бетонных конструкций
2.1.1.1. Измерение прочности бетона
Экспертами произведены измерения скорости распространения ультразвука в монолитных железобетонных конструкциях с целью определения средней прочности на сжатие, класса и марки бетона.
Измерения производились ультразвуковым тестером УК1401 (Сертификат об утверждении типа средств измерений RU.C.34.002.А № 10778), согласно ГОСТ 17624-87 «Бетоны. Ультразвуковой метод определения прочности». Число и расположение контролируемых участков на конструкциях установлены с учетом требований ГОСТ 18105-86 «Бетоны. Правила контроля прочности».
По выполненным измерениям произведены расчеты средней прочности бетона, определены марка и класс по прочности бетона на сжатие. Результаты занесены в таблицу
Все бетонные конструкции выполнены из бетона марки
М150 и классом по прочности на сжатие В10.
Измерение уровня влажности бетона
Уровень влажности измерялся электронным измерителем «Влагомер - МГ4У», предназначенным для неразрушающего контроля влажности строительных материалов по ГОСТ 21718 и ГОСТ 16588. Сертификат соответствия № 0000923, действителен до 14.06.2010 г.
Результат измерений - процентный уровень влажности монолитного железобетона находится в пределах нормы. Наибольший показатель - 4%.
2.2. Надземная часть здания
2.2.1. Наружные ограждающие конструкции помещений выполнены из глиняного обыкновенного полнотелого кирпича толщиной от 380 до 510 мм. При проведении экспертизы выявлены дефекты:
- Кирпичная кладка имеет частичные разрушения по всему периметру здания: по нижней части кладки и по карнизной отделке
- Нижняя часть кладки по причине некачественной отмостки (или ее отсутствия в какой-то период времени) покрыта плесенью, мхом;
- Кирпичная кладка нижней части имеет повышенный уровень влажности от 10,5 до 14,2% в пятиметровой зоне слева от входа в здание;
2.2.2. Кровля
Кровля здания - мягкая рулонная из 3-х слоев рубероида на битумной мастике, утеплитель - пенобетон.
При проведении обследования выявлены дефекты:
- По оси Г - Г в области наружной лестницы подъема на крышу, по причине продольной выемки, образуются скопления воды;
2.3. Внутренняя часть здания
- В результате протечек, по всей видимости, происходивших ранее, до ремонта кровли, внутренние поверхности стен имеют места поражения плесенью, высолы и шелушения;
- Имеют место растрескивания штукатурного слоя и межплиточных швов перекрытия;
- Частичное разрушение кирпичной кладки подпольных каналов;
- На полу отсутствует местами метлахская плитка;
Экспертная оценка состояния помещения
В зависимости от количества дефектов и степени повреждения, техническое состояние строительных конструкций оценивается по следующим категориям (см. Гл. 3 «Термины и определения» СП 13-102-2003).
Техническое состояние фундамента - работоспособное.
Техническое состояние наружных несущих ограждающих конструкций - ограниченно работоспособное, по причине снижения несущей способности конструкций в результате повышенного уровня влажности, частичного разрушения кладки и выветривания ее швов.
Техническое состояние кровли работоспособное.
Техническое состояние внутренней части несущих ограждающих конструкций, внутренних перегородок и пола работоспособное.
Техническое состояние покрытия работоспособное.
4. Поверочные расчеты
Теплотехнический расчет ограждающих конструкций здания
5. Выводы
В ходе проведения обследования выявлены следующие основные дефекты:
- Нижняя часть кирпичной кладки (от 30 до 80 см) имеет выветривания растворных швов;
- Кирпичная кладка имеет частичные разрушения по всему периметру здания: по нижней части кладки и по карнизной отделке;
- В результате нарушения технологии выполнения отмостки по оси А - А, имеются ее растрескивания, застой воды;
- Нижняя часть кладки покрыта плесенью, мхом;
- Кирпичная кладка нижней части имеет повышенный уровень влажности от 10,5 до 14,2% в пятиметровой зоне слева от входа в здание котельной;
- В результате протечек внутренние поверхности стен имеют места поражения плесенью, высолы и шелушения;
- Частичное разрушение кирпичной кладки нижней части стен по осям 6 - 6 и Г - Г;
- Частичное разрушение кирпичной кладки подпольных каналов.
Проведенное диагностическое обследование состояния строительных конструкций здания по адресу: Московская область показало:
После выполнения работ по ремонту участков кирпичной кладки, имеющих частичный объем разрушения, укрепления швов, возможно обеспечить надежность, устойчивость здания в целом и возможность его продолжительной эксплуатации;
На основании данных, полученных в результате обследования, в целом, техническое состояние здания котельной, в соответствии с положениями СП 13-102-2003, оценивается как работоспособное.
- Экспертиза котельной - Строительное обследование здания котельной